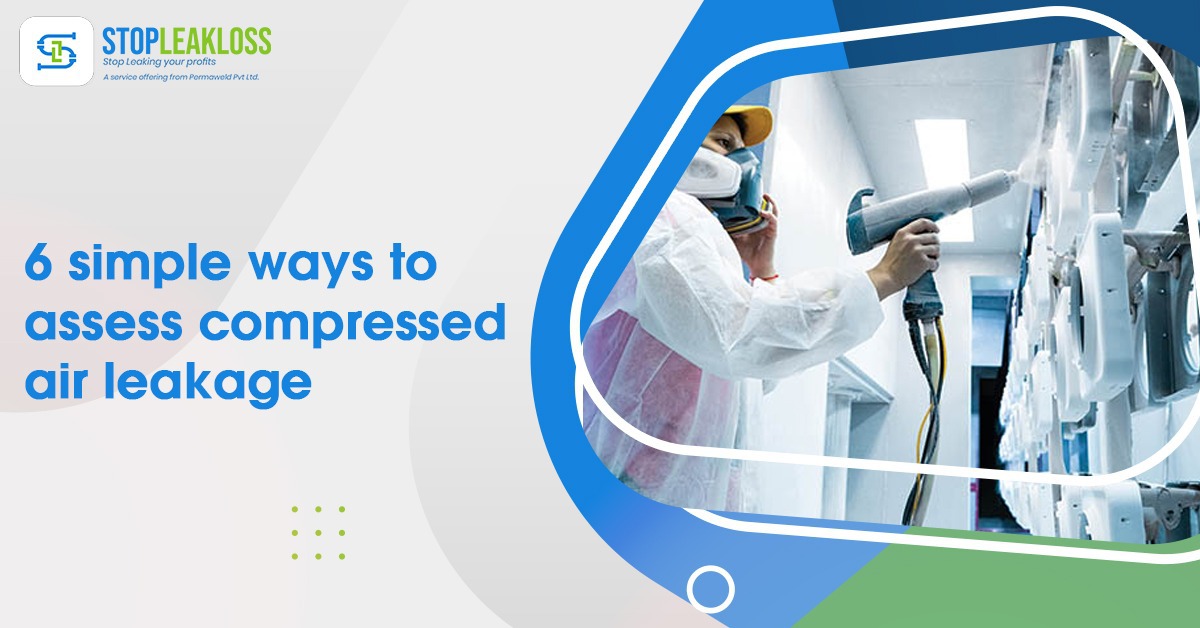
6 Simple Ways to Assess Compressed Air Leakage
Eliminating compressed air waste caused by compressed air leakage is one of the most effective methods to increase the efficiency of a compact air system. But, how much air do you let out? To answer this question, you must measure your leakage flow or conduct some form of inspection that will allow you to produce a price tag for the cost of the waste. Here are six easy methods:
Flow metre
A correctly placed flow metre can quickly measure compressed air leakage. There are so many options for these gadgets at such low rates that there is no excuse to have one. Choose a moment when there is no production in the plant and observe what flow is identified. The chances are that this flow primarily leaks, and it accounts for more than 30% of the total average airflow generated by your compressors.
There is a simple technique to assess the amount of compressed air leakage in the system for compressors that employ start/stop controls. When there are no demands on the system, this approach entails starting the compressor (when all the air-operated end-use equipment is turned off). Then, various measures are gathered to calculate the average time it takes to load and unload the compressor. The compressor will load and unload because the air leaks will force the compressor to cycle on and off as the pressure reduces due to air escaping via the leaks. (compressed air leakage)
Duty Cycle of the compressor:
If you don’t have a flow metre and your compressors are in load/unload mode, you can estimate the leakage flow by timing both the load and unload cycles during a period when no production is taking place. The loaded duration divided by the compressor’s entire cycle time (laden plus unloaded) yields a fraction that may be used to compute the leakage flow roughly. Take this fraction and multiply it by the cfm rating of the operating compressor to find out how much air is flowing. For example, the duty cycle of a 100 cfm compressor with a loaded time of 1 minute and an empty time of 4 minutes is 1/(1+4) = 0.2 for an. As a result, the projected flow rate is 20 cfm.
Rpm of Compressor – If your compressor is a VSD and does not start and stop during non-production periods, you may get a reasonable approximation of the leakage flow by reading the rpm during leakage and dividing it by the rpm at maximum flow. The result is a fraction multiplied by the compressor’s full load cfm to get the same effect as the previous calculation. (compressed air leakage)
Compressors’ Drawdown Test -–
If your compressors only operate in modulation mode, a particular drawdown test must be performed during non-production. The entire volume of the system storage capacity must be estimated for this test by inventorying the linked storage receivers and large pipework. Once the book in cubic feet is known, it is pretty simple to determine the flow during non-production by noting the time it takes for the pressure to fall to 50% when the compressor is switched off and then inserting it into a unique formula.
Compressed air leakage Tests through ultrasonic
Some plants never go into a state of dormancy. If this is the case, the only solution is to conduct a complete leakage survey with an ultrasonic detector. The cost of these devices has decreased over the years, with some costing less than $1,000; therefore, there is no excuse for not having one in-plant. Most leak detectors come with a smartphone app that allows you to estimate the leakage flow based on the db level of the sound and write a compressed air leakage report replete with images and explanations. It is pretty usual for a leak detection endeavour to pay for itself after only a few hours of work.
Identification (including labelling), tracking, repair, verification, and staff engagement are essential components of an effective compressed air leakage prevention programme. All establishments with compressed air systems should implement a rigorous leak detection procedure. In addition, a cross-functional committee of decision-making members from production should be constituted.
A leak prevention programme for compressed air leakage should be part of a more extensive programme to enhance compact air system performance. After the leaks have been identified and corrected, the system should be re-evaluated.
[…] Because proper air compressor maintenance is vital, we highly suggest you choose an air compressor from a reputable brand. The top air compressor brands on the market will provide specialist maintenance services and long-term service contracts. In addition, you should inquire whether the manufacturer has any data collection or intelligent monitoring technologies incorporated into the compressor. […]