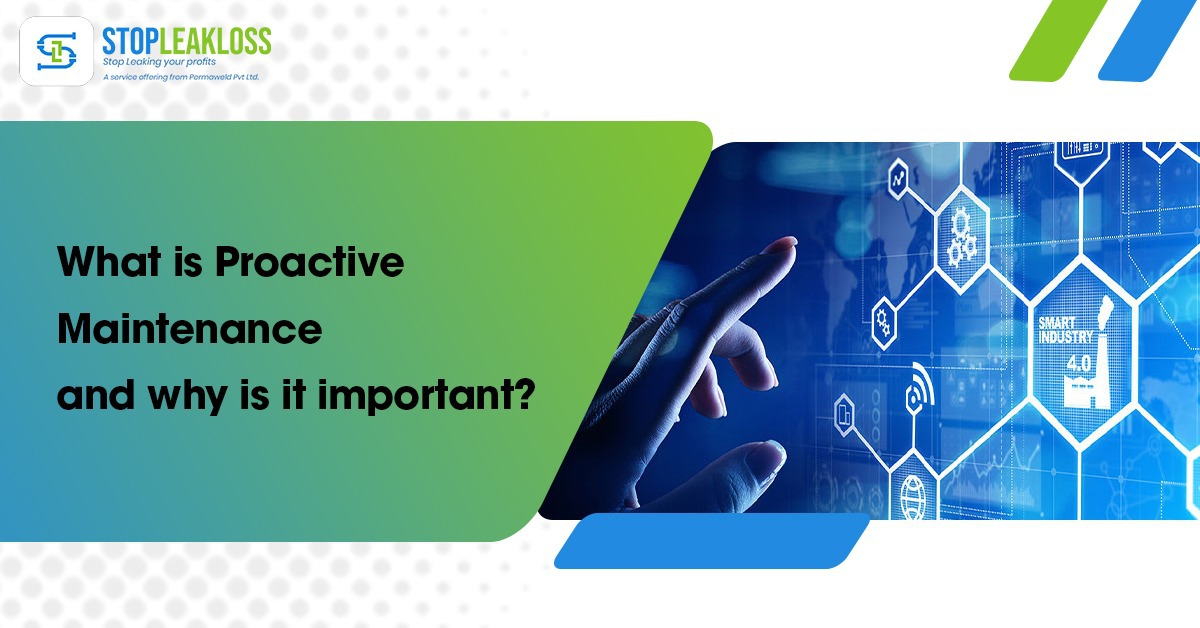
What is Proactive Maintenance, and why is it important?
What is proactive maintenance?
Proactive maintenance is a preventative maintenance method that addresses the root cause of underlying equipment issues. Proactive maintenance aims to decrease unexpected downtime, equipment failure, and the dangers of running damaged equipment.
Overview
The adage “if it ain’t broke, don’t repair it” appears to be a reasonable way to deal with maintenance chores. That is until you see the colossal expense for rapidly repairing essential assets that have broken down. In addition, unplanned downtime not only hurts productivity but also exposes workers to safety hazards due to defective equipment.
The influence of equipment reliability on overall plant performance has shifted organisations to more proactive maintenance practices. While wear and tear on equipment are unavoidable, investing time and resources in preventative maintenance may dramatically extend the life of an asset.
The saying “if it ain’t broke, don’t fix it” appears to be realistic to maintenance tasks. That is until you consider the massive cost of quickly fixing critical assets that have broken down. In addition, unplanned downtime not only reduces production but also exposes workers to safety risks due to faulty equipment.
Types of proactive maintenance
Proactive maintenance is any form of maintenance that is done before any significant breakdowns or failures occur. The criteria that would trigger proactive maintenance activities bring about several types of proactive maintenance.
Preventive maintenance (PM)
One of the most popular types of proactive maintenance is preventive maintenance (PM). Maintenance actions are carried out under a PM programme to keep assets in excellent operating order. The frequency of conducting PM tasks might be:
- Calendar-based.
- Usage-based.
- Predictive or based on past data analysis.
- Prescriptive or as decided by logical software.
Condition-based maintenance (CBM)
Other methods of proactive maintenance monitor asset performance regularly. For example, the frequency of tracking assets can be real-time, as in condition-based maintenance (CBM), where sensors monitor equipment performance to identify possible problems before they occur.
Scheduled and routine maintenance
Alternatively, the frequency of tracking equipment performance can be manually defined. The maintenance planner can establish schedules or processes for checking equipment performance during planned maintenance or routine maintenance.
Proactive care may take many forms, and plants typically use a combination of these measures. The most appropriate maintenance will depend on the type of equipment and should be carefully determined to ensure the most efficient method is utilised.
Benefits of proactive maintenance
As proven by the preceding instances, proactive maintenance allows a corporation to save money in the long term. Savings are realised through reducing downtime and improving equipment dependability and availability. Equipment can also be anticipated to stay operational for extended periods if degradation is controlled by proactive maintenance.
Another advantage of undertaking preventative maintenance is a lower likelihood of safety-related mishaps. A maintenance strategy would make it safer to run equipment, particularly that which has the potential for catastrophic failure. This is especially visible in how oil and gas businesses execute severe maintenance efforts to guarantee that harmful chemicals are confined.
The disadvantage of proactive maintenance
The advantages of preventive maintenance need expenditures in both time and finances. The upfront expenditures necessary are frequently the deterrent for facilities to switch to maintenance practices. Proactive maintenance techniques should be planned carefully to ensure that they are cost-effective and useful to the facility.
Example of proactive maintenance
Changing the oil on a car is a realistic example of preventive maintenance. Engine degeneration caused by improper lubrication is a headache to repair if it can be repaired at all. What appears to be a little expenditure of changing the oil after a set number of miles adds years to the life of a vehicle.
Consider the National Ignition Facility (NIF), the biggest and most energetic facility ever built, as an example of preventive maintenance on a bigger scale. Since 2011, a mix of maintenance efforts, including condition-based maintenance, has allowed NIF to save almost $3.5 million as of 2017. The majority of the savings were related to avoiding downtime and needless emergency repair actions.
Conclusion
The term “proactive maintenance” refers to various measures that may be implemented to prevent unexpected downtime and equipment breakdowns. Significant savings can be realised by correctly investing resources in better plant performance and safety.