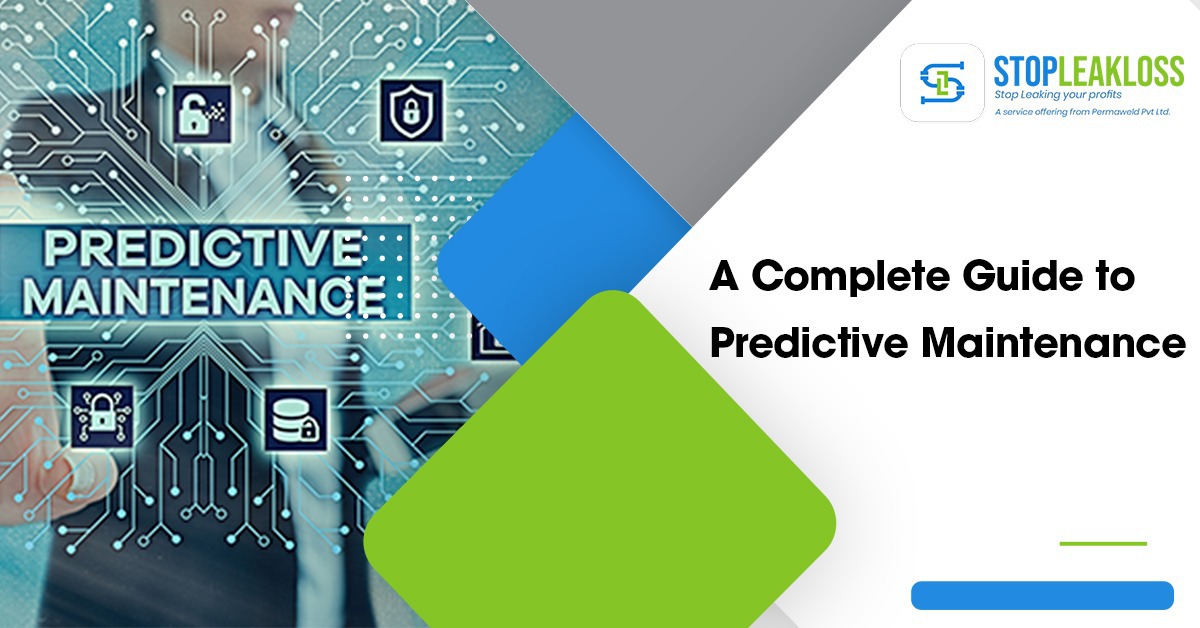
A Complete Guide to Predictive Maintenance
To determine whether predictive maintenance is a technique that might benefit your business, you must first understand what it is, how it works, what its benefits and drawbacks are, and how to develop a predictive maintenance programme.
You’ve come to the correct spot if you’re seeking a resource that can answer all of those questions and more.
What is predictive maintenance (PdM)?
Predictive maintenance is a proactive technique that uses condition monitoring instruments to detect different degradation symptoms, abnormalities, and equipment performance concerns. Based on such measures, the organization may use pre-programmed predictive algorithms to anticipate when a piece of equipment would break, allowing maintenance work to be completed just before it fails.
Predictive maintenance seeks to maximize the use of your maintenance resources. Knowing when a particular part will fail allows maintenance managers to schedule maintenance work only when required, reducing unnecessary maintenance and eliminating unexpected equipment breakdown.
When done correctly, predictive maintenance reduces operating costs, decreases downtime concerns, and enhances overall asset health and performance.
How does predictive maintenance work?
The primary benefit of predictive maintenance is the ability to plan work based on the existing state of the asset. However, determining the actual condition of complex support is anything but simple.
PdM has three key components to track asset status and advise technicians about impending equipment failures:
installed situation
-monitoring sensors transmit real-time performance and machine health data.
IoT technology facilitates connectivity between devices, software solutions, and cloud technology, thus assisting in collecting and analyzing massive volumes of data. Predictive data models are fed with all of that processed data to spit forth failure predictions.
Let’s take a deeper look at all of the primary components described above to understand better how predictive maintenance works.
- CM technology and predictive maintenance techniques
Condition-monitoring sensors and equipment of various types can be installed/retrofitted. Electrical currents, vibrations, temperature, pressure, oil, noise, corrosion levels, and other parameters may be measured.
The sensors you choose will be determined by the type of assets on your PdM and what you wish to track.
Another advantage of having condition-monitoring sensors is that you may get an accurate depiction of what’s going on within the asset without disrupting work. In other words, you don’t have to halt the asset and disassemble it to undertake physical inspections.
- The role of IoT technology
It is one thing to collect data; it is another to evaluate and apply the data for its intended purpose. The sensors described previously can gather and distribute data by utilizing Internet of Things (IoT) technology. PdM largely relies on these sensors to connect the assets to a central system that archives the data that comes in. These central hubs are powered by WLAN or LAN connection or by cloud technologies.
Depending on how the system is configured, the assets can communicate, collaborate, analyze data, offer corrective action, or take direct action.
- Applying predictive algorithms
Building predictive (a.k.a. prognostic) algorithms are the most critical (and possibly challenging) aspect of predictive maintenance. In essence, you must create a model that considers a wide range of factors and how they interact and affect one another — with the ultimate objective of predicting machine failures.
The more variables you have at your disposal, the more accurate your models will be. As a result, developing predictive models is an iterative process. The first models must be based on asset history maintained in a CMMS or file cabinets, human observations, FEMA analysis, currently accessible internal sensors such as accelerometers and flow metres, and similar sources. It may even be necessary to initially install condition-monitoring sensors and run them for some time to acquire baseline data and complete the initial prediction models.
Here’s how the algorithms operate without getting too technical. They operate according to a set of established rules that match the asset’s present behaviour to its predicted performance. Deviations are a sign of steady degradation that will lead to asset collapse. The algorithms attempt to anticipate failure spots based on deviations, present operating circumstances, prior failure data, and other variables integrated into the data model.
Pros and cons of predictive maintenance
Predictive maintenance, like any other maintenance technique, has its advantages and disadvantages:
The major reason predictive maintenance isn’t more frequently used is that it has a somewhat high entry barrier. Purchasing and installing condition monitoring equipment, developing predictive models, and integrating everything with a CMMS or other specialist software might all demand significant upfront expenditure. Furthermore, constructing models and algorithms takes specific knowledge, which is frequently outsourced. Because of this, PdM can be difficult to set up and maintain.
Despite these drawbacks, predictive maintenance is likely to rise, indicating that the benefits exceed the drawbacks. As a result, we won’t repeat them here because they are well described in the image above. The final conclusion is that predictive maintenance may yield a high ROI in the long run, making it a risk worth taking.
Combining predictive maintenance with CMMS software
Over time, CMMS has aided the transition from manual operations and reactive maintenance to more proactive tactics such as preventive and predictive maintenance.
Today, it’s reasonable to assume that CMMS is at the forefront of PdM applications. Here are a few of the causes behind this.
CMMS provides the initial data to get PdM rolling
Before PdM deployment, the information obtained over time about asset performance helps build the beginning point and first dataset. Though alternative sources, such as hard copy maintenance records, exist, CMMS will give the most comprehensive and easily accessible historical information.
CMMS integrates with PdM technology to generate automatic tasks
When sensors identify an asset functioning outside of established parameters, a contemporary CMMS can immediately issue an alarm or a work order. These signals inform the maintenance staff to take preventive measures before the equipment breaks and causes a major disaster.
In summary, even though PdM creates very accurate asset data, its applicability is restricted until it is paired with a CMMS. On the other side, CMMS cannot assess or forecast machine health on its own.
Users gain a powerful, necessary solution for a contemporary maintenance management team by integrating both technologies. Predictive maintenance alerts you when certain maintenance activities must be performed, and CMMS assists you in managing your resources and incorporating those jobs into your maintenance calendar.
CMMS facilitates data interpretation
Although PdM tools provide valuable insights about asset condition through vibration, lubricant, heat, oil analysis, etc, the data generated is enormous and cumbersome for humans to manage manually.
With the right CMMS, users easily understand “snapshot” of the data that’s coming in.
CMMS serves as a central organizational tool
CMMS gathers various asset-related data and presents it in a single platform that provides a more comprehensive equipment “status report.”
PdM, for instance, will provide the raw data from the machines. CMMS, on the other hand, incorporates data from other modules such as asset history, inventory, spare parts management, manpower management, repair scheduling, and more, allowing maintenance departments to make better-educated choices.
[…] thermography is its application in condition monitoring. Infrared Thermography in Condition Monitoring aids in the identification of a wide range of difficulties, including heat-related concerns, […]