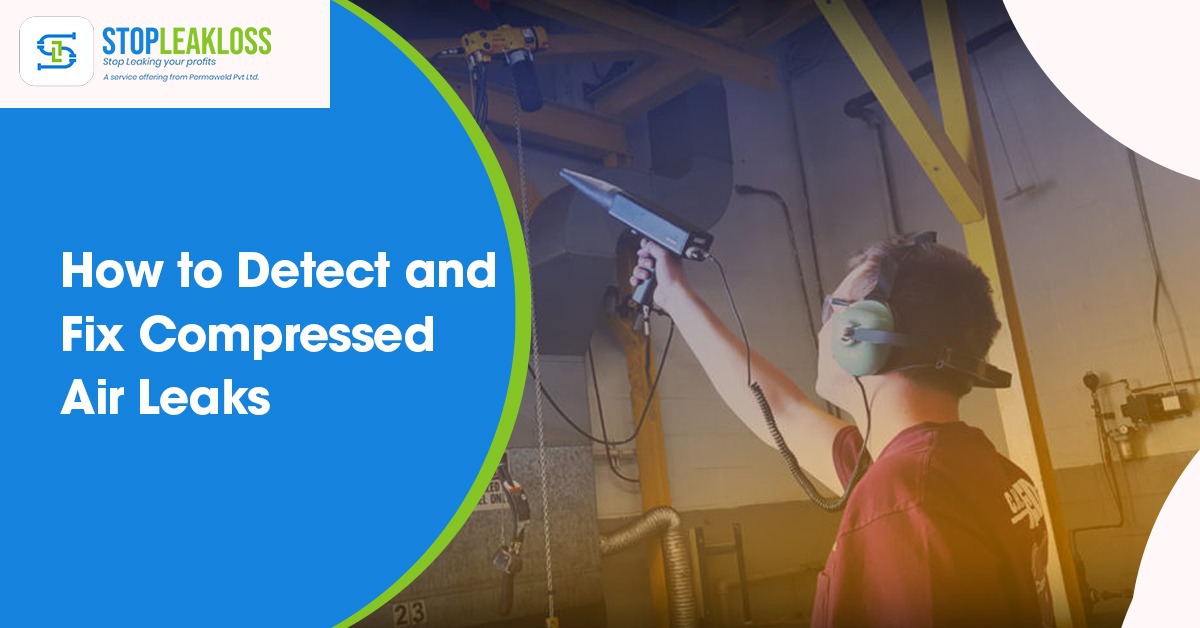
How to Detect and Fix Compressed Air Leaks
How to Detect Leaks and Fix Them
Compressed air leaks may quickly become a substantial source of lost energy in an industrial plant, losing up to 30% of the output of a compressor. But how can you identify leaks if you can’t see them? Most experts believe that using an ultrasonic sound detector is the best technique to identify leaks. This gadget detects high-frequency hissing sounds associated with air leaks and employs a range of visual and aural clues to pinpoint the leak’s location.
Under the incorrect conditions, compressed air leaks may be financially catastrophic. The most frightening feature of compressed air leaks is the length of time they may go undiscovered. Consider research conducted by the Compressed Air & Gas Institute. They discovered that a single 14-inch leak in a compressed air line might cost a business anywhere from $2,500 to $8,000 per year. The terrifying aspect is that you could not even be aware of it.
Leaks not only raise energy costs but can also disrupt system operation. For example, leaks force compressors to work more to generate the same volume of compressed air. This extra stress can jeopardise equipment durability, increase running hours, and raise total lifespan costs.
If left untreated, persistent air leaks may shorten the life of your air compressors. The first step is to recognise the danger. The second step is to address and resolve the problem.
Detecting Compressed Air Leaks through Ultrasonic leak detection
Due to its capacity to adapt to several leak detection settings, ultrasonic leak detection is one of the most adaptable types of leak detection. Its acoustic sensor zeroes in on noise changes to pinpoint the location of mid-to-large-sized leaks. Ultrasounds can locate leak sources by focusing on the loudest sound level since they are short wave signals that are directional in transmission. Because the signs in the audible range are filtered out, ultrasonic detectors are often unaffected by background noise.
How to fix Compressed Air Leaks
- Leaks are widespread at joints and connections. Stopping leaks can be as easy as tightening a connection or as sophisticated as replacing damaged equipment such as couplings, fittings, pipe sections, hoses, drains, and traps.
- Leaks are frequently caused by faulty or incorrectly placed thread sealant, which may be remedied by adequately installing equipment with the proper thread sealant.
- Non-operational equipment can also be a cause of leakage. Equipment no longer in use should be disconnected from the distribution system using a valve.
- Lowering the compressed air system’s demand air pressure can also help to decrease leaks. The lower the pressure difference across an orifice or leak, the lower the rate of flow, resulting in a reduced leakage rate.
Once leaks have been detected and repaired, the compressor control system should be re-evaluated to maximise savings. Do you want to set up a leak prevention programme to save your industrial plant money on costly repairs? Then, get in touch with Stopleakloss right away!
How to Detect Compressed Air Leaks and Avoid Problems in the Future
The first step in preventing losses from compressed air leaks is to determine the source of the problem and then take corrective action. Unfortunately, air leaks can lie undiscovered for years, resulting in lost energy bills for an extended period before the damage can be remedied.
Fixing compressed air leaks may appear costly to some managers at first. Still, when it comes to yearly savings, maintenance investments significantly surpass the cost of losing tens of thousands of dollars due to lost airflow.
The first step in preventing losses from compressed air leaks is to determine the source of the problem and then take corrective action. Unfortunately, air leaks can lie undiscovered for years, resulting in lost energy bills for an extended period before the damage can be remedied.
Fixing compressed air leaks may appear costly to some managers at first. Still, when it comes to yearly savings, maintenance investments significantly surpass the cost of losing tens of thousands of dollars due to lost airflow.
Once you’ve identified leaks and made any required repairs, you’ll want to prevent other leaks from happening.
One method requires personnel to do frequent leak checks using ultrasonic leak detectors. In addition, they should document the position and magnitude of any leaks, which will aid in determining the cost of the leaking.
If you don’t have an ultrasonic leak detector and are worried about the cost of setting up a leak monitoring and prevention system, hiring a third party to do the audit might help you justify the expense. Furthermore, the cost of obtaining an ultrasonic leak detector may be justified because it will allow you to execute audits with greater precision, resulting in lower lost energy costs.
[…] boards, rotating motor monitoring, boiler operations, and steam system monitoring may benefit from thermography condition monitoring. This is a technique for pinpointing the specific site of a malfunction in a […]