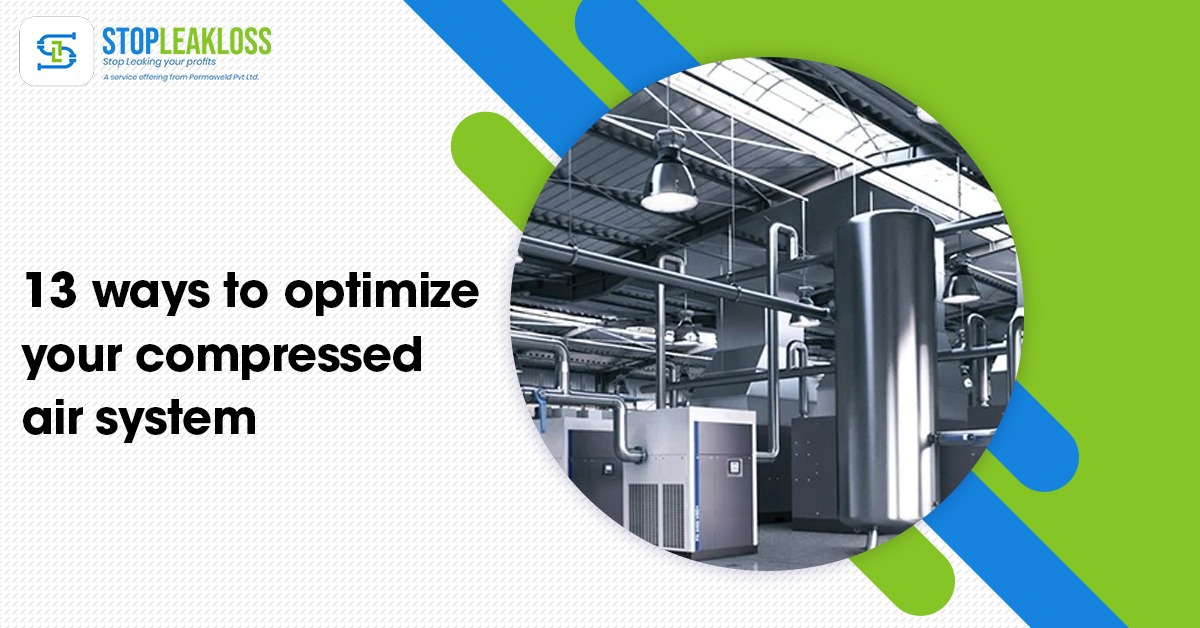
13 Ways to Optimize your Air Compressor System
Air compressor system- You may also have heard that compressed air is one of the most costly utilities in a commercial plant. It’s true that compressed air is a terrible way to transmit power to a commercial gadget or device if you need advanced performance. That being said, it’s miles not going that withinside the call of power performance alone. You will convert all your commercial gear and gadget to direct-force electricity. Compressed air will by no means disappear from commercial plants; it’s miles an utterly practical utility.
Compressed air machine expenses range widely. This is because the performance of structures is frequently ignored, as they’re often extra critical problems in strolling a machine. (Chief amongst those are preserving the stress at a steady, dependable stage and keeping good enough air exceptional so that manufacturing runs smoothly.) Sometimes structures run at high-quality performance; at different times, elements associated with gadget characteristics, machine design, waft characteristics, and renovation ranges can purpose matters to head very wrong. (air compressor system)
The accurate information is you could do something positive about it.
1. Get focused schooling
What you and your personnel don’t recognize will harm you regarding compressed air. It may be very unusual to see amazing looks on people’s faces after discovering how much of its miles cost to run their compressed air structures and how little mechanical power they get hold of for the expenditure. Compressed air machine focus schooling is the quality first step in optimizing your machine with the aid of coaching you to apprehend your gadget and the way it’s strolling. This expertise is a critical key to getting your expenses in line. (air compressor system)
2. Monitor your compressed air machine
To take care of your compressed air machine expenses, you must degree your machine. A machine that isn’t always measured can’t be efficiently managed. Creating a baseline is critical in expertise in demanding situations that enhance your machine’s performance, exceptional air balance, and reliability. To screen, you have to degree key parameters like stress, waft, power, and dew factor overtime. Once collected, those records want to be analyzed by peers if there are any problems.
More and different factories enforce everlasting tracking in their compressed air structures so that machine parameters can continuously be monitored and adjusted. This is proper practice; however, appropriate consequences can nevertheless be acquired by using transient metering. The dimension and evaluation of your machine the usage of the offerings of a certified compressed air auditor can factor you withinside the
3. Implement green compressor and dryer manipulate
Are your compressors and dryers being managed efficiently? In what manipulate mode are they working? It is uncommon to discover a compressed air device operator with the solution to those questions. The manipulation of the air compressor systems and related systems like air dryers could be essential to the performance and reliability of the device.
Concerning person compressor controls, there are numerous not unusual place modes of operation, with a few extra greens. Not unique place modes are start/stop, inlet modulation, load/unload, variable ability manipulation, and variable speed. Air dryer conduct is usually forgotten in a device control effort, particularly wherein desiccant fashion dryers are used. If your device has non-biking refrigerated dryers, then you could lessen electricity prices with the aid of using ensuring that any spare dryers are grown to become off if their related compressors aren’t running.
For desiccant dryers, dewpoint controls may substantially lessen the dryer purge call for if the dryers are experiencing flows that can be much less than rated conditions. It isn’t always unusual to locate desiccant air dryer purge making up the most significant factor of the compressed air call for in a business plan, in a few severe instances even extra than the call for ate up with the aid of using manufacturing machinery.
4. Boost performance through system substitute
The compressed air enterprise has been modified for the better. Manufacturers are very conscious that their clients are interested in electricity performance, so they have redesigned their system to be extra green. However, when it comes time to do a luxurious principal overhaul for your antique air compressors systems, maintain in thoughts that the antique system might not be as much as cutting-edge standards. Rather than repairing an inefficient antique compressor or compressor motor, it can be for your first-class hobby to examine changing the system with a state-of-the-art extra green unit. This substitute can reduce working prices and pay for the substitute prices in a brief duration of time.
5. Install Repository Listener
Storage sinks allow you to improve the overall efficiency of your system in several ways. For example, a central air receiver in the compressor room can enhance compressor load/unload control efficiency. In the past, it was thought that lubricated screw compressors required only about 1 gallon of capacity per cubic foot per minute of rated compressor capacity. But if the goal is efficiency, this turns out to be wrong. Adding more than 5 gallons per cubic foot per minute has excellent benefits in reducing the impact of high-speed cycling screw compressors.
This demonstrates adding an accumulator to make the compressor more like an “ideal compressor”.
If production equipment is subjected to local pressure fluctuations, a storage tank protected by a check valve can be installed to protect the equipment from temporary low-pressure transients. This can avoid the need to increase the system pressure to compensate.
6. Compressed Air Pressure Reduction
The higher the discharge pressure, the more energy the air compressor consumes. Typically, at about 100 psi and constant flow, the required compressor output increases by about 1% for every two psi. So, if you can reduce this exhaust pressure, you can get some savings in your compressed air system. Why is there such high pressure in the system? There can be several reasons, including end-user requirements, pressure drop, compressor control characteristics, etc. Often, system operators do not know the answer to the question. (air compressor system)
In many cases, the pressure is set to a certain level because it is rated for the compressor. It is essential to know the actual pressure requirements and be aware that overpressure will cause the compressor to draw more power than needed without further manufacturing improvements. If you think there is no good reason for the high pressure, reduce the stress.
7. air treatment efficiency improvement
Air compressors system produce hot, humid and oily air that must be conditioned not to contaminate downstream machinery or processes. The compressed air is dried using air dryers and is typically filtered to remove contaminants. However, compressed air treatment equipment can be a significant source of energy loss through purge loss (for desiccant dryers), electrical power consumption (refrigerated dryers), pressure loss (causing the compressor to consume more power), or through excessive drainage while removing the captured liquids from the system.
The selection of more efficient air dryers that use less power through efficient design, low or no purge flow, and the lower designed pressure differential is a good energy efficiency measure. Airless condensate will reduce the compressed air waste that might be occurring if cracked open manual drains or timer style drains are typically used to expel liquids from the system. Every psi reduction in pressure differential or reduced cfm of wasted compressed air translates to less energy consumed at the air compressors system. (air compressor system)
8. Modernization of the Plant Pipeline
Small compressed air piping can lead to flow restrictions in the compressed air system, compensated by increased compressor discharge pressure. Often, the size of the collector system of the compressor and distribution pipelines was determined many years ago. Over time, installations increased, and compressed air requirements increased when the original piping became too small. (air compressor system)
As part of the system optimization process, you should measure the pressure drop across the compressed air system to determine a problem. Pipe modifications, such as system loops, may improve the situation or require increased pipe size. A sound system should have no more than 10% pressure drop across the entire compressor room to the final piping outlet. In a good plan, the drop is no more than 2%. (air compressor system)
9. Reduced pressure loss of parts
An important and important point to check is the pressure difference between the pressure drop in the pipeline and the actual end use of the compressed air. It is common to see the biggest pressure differential occurring in the “Dirty Thirty,” i.e. the last 30 feet of pipe. In that last section of piping, there may be undersized filters, regulators, lubricators, connectors, and hoses, all elements that can contribute to significant pressure differential. (air compressor system)
This differential can also be inside the production machinery itself. When major pressure differentials occur in this section of the system, the discharge pressures at the air compressor end must rise to compensate, increasing the power costs. Care and attention to sizing these components for low-pressure differential at peak flows can often cost only a few hundred dollars but yield thousands of dollars in annual savings at the air compressors system. (air compressor system)
10. Implement leakage detection and repair
On average, about 2530% of the compressed air produced by the air compressor systems never makes it to the end-user. If there is no leakage detection and repair program in the plant, this number can be much higher, and in extreme cases, up to 80% of the average air demand can be leaked. The repair of compressed air leaks is one of the easiest ways to gain energy savings in a compressed air system – all you need in most cases is a keen sense of hearing, some time, and a few wrenches. And if better tools are used, like implementing ultrasonic leak detection into a regular maintenance program, improved results can be achieved.
A good goal is a leak rate of 10% of the average compressed airflow. It is important to ensure that the air compressor systems at the other end are well controlled and dynamic to make the most of leaks. Reducing the leak flow reduces the power consumed by the air compressor system. Moreover, this reduced flow minimizes the pressure drop across all system constraints.
11. Reduction or Elimination of Improper Use
Misuse of compressed air is easy to implement. However, with proper training, your staff will realize that the easy way out may not be in your best interest because of the high cost of compressed air. Many compressed air activities can be done more efficiently using other energy sources. These may include purging, cleaning, cooling, pumping, vacuuming, stirring, material movement, air motor actuation, and liquid spraying.
When optimizing a compressed air system, these potentially inappropriate compressed air usages are identified and analyzed during air system studies. The lifecycle cost is then compared to other methods of doing the same thing. In some cases, users cannot be eliminated but can be optimized by supplying a lower pressure, discontinuing use when not needed, or redesigning less compressed air.
12. Artificial Demand Decrease
When equipment and processes receive compressed air at higher pressures than designed, they typically consume more volume but do not provide additional production benefits. For example, pneumatic cylinders use more air at higher pressures because they require more air to fill. Likewise, the blower uses more pressure to expel the air at higher pressures. This translates to more increased total flow and higher compressor power consumption.
Reducing plant pressure by reducing compressor discharge pressure can yield savings, but so will the use of pressure/flow control devices that regulate the absolute main plant pressure to only the minimum level required by downstream equipment. And local, well-sized regulators that have been carefully selected to handle without excessive drop can reduce the artificial demand at individual end-users. (air compressor system)
13. Use incentive programs
Compressed air optimization can be implemented using low-cost or no-cost measures, but significant expenditure is usually required to achieve the best results. Your local utility or energy organization can help improve your compressed air system with financial incentives to save energy. Some of these organizations support basic energy studies or more detailed full audits and fund a significant portion of compressed air power generation projects. These organizations may have information resources and support staff to help you apply for these funds. It is worth asking about the capabilities of the plant.