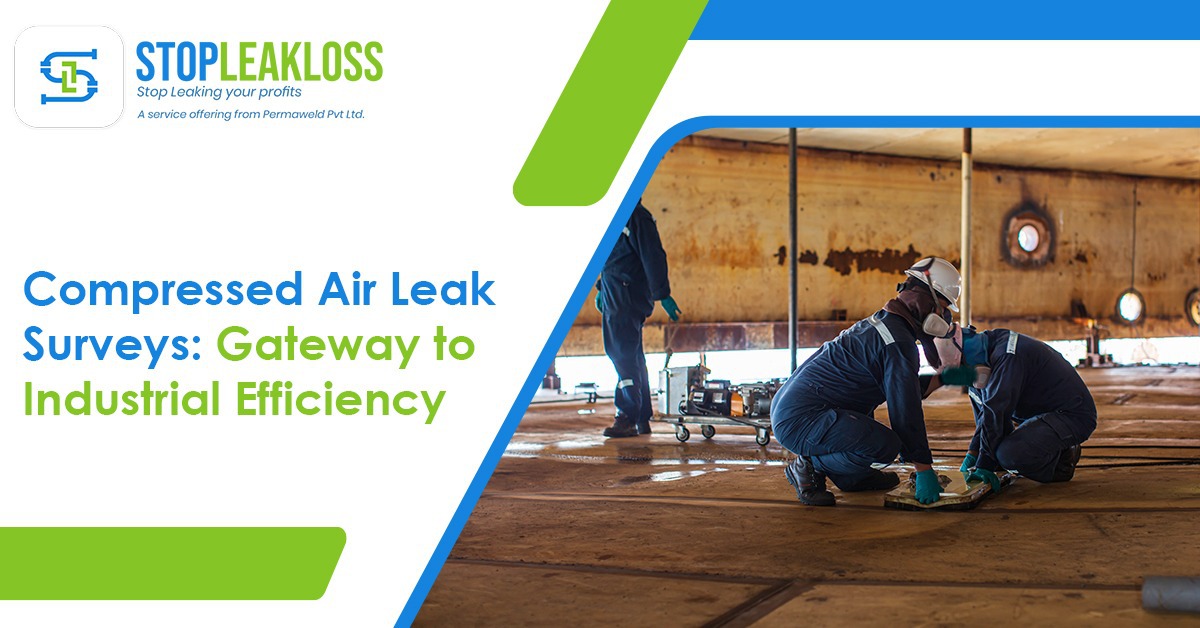
Compressed Air Leak Survey: Gateway to Industrial Efficiency
Introduction
Making compressed air can be answerable for as much as 30% of a production line’s general energy utilization. Squandering some portion of this energy through releasing compressed air pipework is essentially discarding cash. Therefore, investigating your compressed air framework is a superb way of beginning the streamlining of your plant or assembling facility. (compressed air leak survey)
One of the easiest and best checks to make your compressed air framework is a compressed air leak survey. The customary electrified steel compressed air pipework is inclined to spill after a couple of years. From studies, most more seasoned pipework frameworks leak on normal 20%-30% of delivered compressed air, so it is clear potential savings are huge. (compressed air leak survey)
One of the most common causes for air leaks in more established galvanized pipework is erosion. This ordinarily happens in the strings at the joints. The consumption makes the line grow, making a compressed air leak. Anyway, there are numerous other normal reasons for leaks in compressed air pipework. Faults include:
- Broken valves.
- Leaks from mechanical harm.
- Leaking hoses or nylon tubing.
- Releasing fast delivery couplings or leaking connections to plants and machinery.
How can compressed air leaks be fixed?
The first and most significant stage in fixing the leaks is recognizing where the leak is, what is causing the issue, and how enormous the issue is. Through an ultrasonic air leak survey, we will ordinarily discover 10s to 100s of leaks in a more established pipework framework. Anyway, most of these will be little and presumably not financially savvy to fix. Ordinarily, 80% of energy can be saved by fixing 20% of the leaks, so these are the ones to zero in on.
Whenever we have confirmed the ones to fix, we can distinguish the necessary parts to fix the issue. These will incorporate substitution valves, hoses, leakage hoses and couplings. We can likewise work out the best fix for harmed and leakage pipework. Current aluminium pipework is undeniably more leak resistant than more established galvanized pipework because of its corrosion resistance, ‘O’ ring seals (giving it better protection from little developments) and lighter weight. It is likewise a lot simpler to fix or modify. (compressed air leak survey)
How to check for compressed air leaks in your factory?
Four easy checks can be done effectively to perceive how big an issue your production line has with a leakage framework.
- When the industrial facility hushes up, would you be able to hear the hiss of compressed air?
- When you are not underway, is your compressor running at times?
- Is the strain perusing on the recipient in the compressor house higher than the tension reading at the uttermost mark of utilization in the processing plant?
- What pressures do your processes require versus the strain that is produced by the compressor?
These are simple ways that you can perform yourself. Nonetheless, appropriately working out the size and scale of the leaks you have in your pipework framework is ideal for bringing in specialists with the right gear and experience to do the task rapidly and proficiently. Air equipment will utilize ultrasonic analyzers to recognize even the tiniest leaks. The equipment is excessively delicate to the point that even a little release can be recognized from many metres away.
We have even identified small air leaks from pipework that is confined to a divider. The equipment can give a proper assessment of the size of the leak so we can work out for every specific leak how much cash is being squandered and what the savings would be if the leak were fixed-giving an incredible payback estimation.
The air equipment compressed air leak survey process.
During the air leak survey process, one goes around your pipework with an ultrasonic air leak detector. The architect recognizes and labels each release, giving it a novel reference, area and size of the break. As a rule, additionally, the trouble spot is also photographed. Then, at that point, compose this data in a report which is presented back to the client. Typically, suggestions regarding which leaks we feel ought to be done and the expense to complete these repairs are also given. The customer can follow recommendations or come up with their own, however continually knowing how much it will cost for the maintenance and how much energy they will save.(compressed air leak survey)
Conclusion
A compressed air leak survey is an efficient way of educating industrial workers about the expenses of compressed air systems and the benefits of efficiency involving several levels of an organization and accomplishing many kWh at a low cost. The high expenses of compressed air and several inefficiencies in industrial equipment are frequently hidden from industrial clients. (compressed air leak survey)
Compressed air leak surveys show maintenance personnel, plant managers, and senior management the costs of compressed air system leaks and how low-cost modifications can result in large electrical energy savings. This encourages employees at all company levels to look for more ways to save energy and money in processes and equipment.