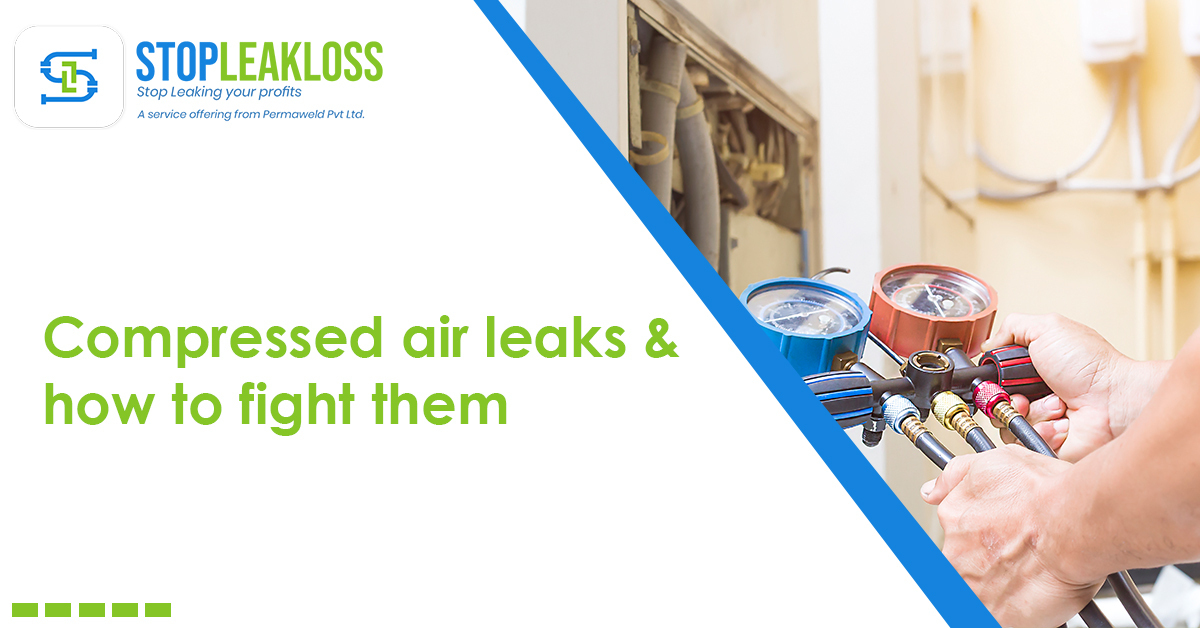
Compressed air leaks and how to fight them
Introduction
Compressed air systems are prone to air leaks. The key is to understand how to detect and repair them, as even a small leak may quickly mount up to a significant bill if left unchecked. Leaks of compressed air are common in all applications. They’re not only common, but they’re also time-consuming to locate and repair. Compressed air accounts for 20-30% of total energy usage in a typical manufacturing operation. Compressed air leakage accounts for 30% of that cost on average.
Detecting compressed air leaks
Compressed air leaks can be detected in several ways:
1. Listen — You can sometimes hear the hissing of a leak as you move around the plant, following the compressed airlines. Regrettably, this isn’t always successful. The audible sound is frequently difficult to notice due to the loudness of an operation, or the pipe is usually near the ceiling and much above the floor. When the plant is not in use, it is ideal for conducting audio leak detection during off-peak hours or weekends.
2. Ultrasonic acoustic detector — This sort of detector detects leaks by picking up high-frequency noise waves. Directional microphones, amplifiers, and audio filters are frequently used in this setup. To see or hear leaks, a visual indication or headphones are utilised.
- A laminar flow is created when compressed air flows through a conduit. This form of flow occurs when all particles are moving in the same direction, and at the same time, when there is a leak in the pipe, the airflow shifts to turbulent flow around the leak.
- Ultrasonic detectors evaluate the noise created by the turbulent air. One of two methods will be used to operate the detector. It will either connect to headphones and generate a sound that will become louder when a leak is detected, or it will feature a screen that will display the ultrasonic waves. When the sound becomes stronger, the wave will change dramatically.
- Thanks to ultrasonic detectors that filter out background noise, leaks can be heard or observed even in very noisy situations.
- This procedure is a quick and accurate way to find compressed air leaks.
How to fight compressed air leaks?
While air compressor leaks may appear to be an unavoidable problem with the equipment, it’s important to realise that they may be prevented and stopped. Some of the ways to fight compressed air leaks include-
- Anything that has the potential to loosen is ripe for an air leak. It’s a good idea to go around your compressed air system regularly and tighten any connection points. If any loose components are visible or felt, tighten them as well. The less compressed air you lose, the more secure your system is.
- Another major source of air compressor leakage is air hoses and tubes. These leaks are a little more difficult to spot, but if you hear a leak and can’t pinpoint where it’s coming from, dab a little soap on the area where you suspect a leak. When your compressor turns on, bubbles will appear around the air leak. Replace the leaking hose or tube with a new one, and your air compressor will be in good working order.
- It’s still a worthwhile improvement that will help your compressor last longer in general. Internally, air compressor motors can become unstable if screws and bolts loosen in internal components. Tightening those internal screws and fasteners will assist cure the problem and eliminate air leaks while you’re at it if you notice any unsteady components or excessive noises emanating from the engine.
- Another key area where you’re likely to uncover a few air compressor leaks is old replacement parts. Air compressor leak points include old filters, lubricators, regulators, flanges, and leaking drains. Repair or replace the old parts as soon as feasible if you can. Even minor maintenance, such as changing the filter, can help ensure that your air compressor runs as efficiently as possible.
- Air compressors must be serviced regularly. Regular oil changes and maintenance are required for an air compressor, just as for a car. Setting up a regular maintenance plan or service schedule with your air compressor supplier is the quickest method to stay on top of maintenance and avoid air compressor leaks. As a result, their service specialists will come out to your facility and perform any essential maintenance. This is a set-it-and-forget-it option that guarantees your air compressor receives the maintenance it requires without causing you too much trouble.
- In addition to a regular repair schedule, regularly having one of your maintenance or facilities employees evaluate your compressors is a smart idea. Even a simple weekly walk around your compressed air system might help you detect air leaks early. The faster you can minimize air compressor leaks, the more money you save. The best approach to keep your factory running smoothly and at the top output is to use smart, energy-efficient compressed air systems. System audits might assist you in achieving your goals. A compressed air leak audit can assist you determine if your system has air leaks or isn’t performing as well as it should. TMI’s specialists use kW and pressure loggers to measure your system accurately and thoroughly, then compare it to industry averages. From there, we’ll be able to pinpoint any issues and make recommendations to assist you in getting your system back up and running. Air leaks are a major source of concern for any plant that uses compressed air, but they may be avoided and halted. You can avoid or eliminate air compressor leaks with a bit of routine maintenance and a few easy repairs and replacements, allowing your facility to operate at full performance.
Conclusion
Compressed air leaks are a regular occurrence, but they’re easy to spot and fix. Therefore, it’s critical to check for leaks regularly and address them as soon as possible to avoid costly repairs.