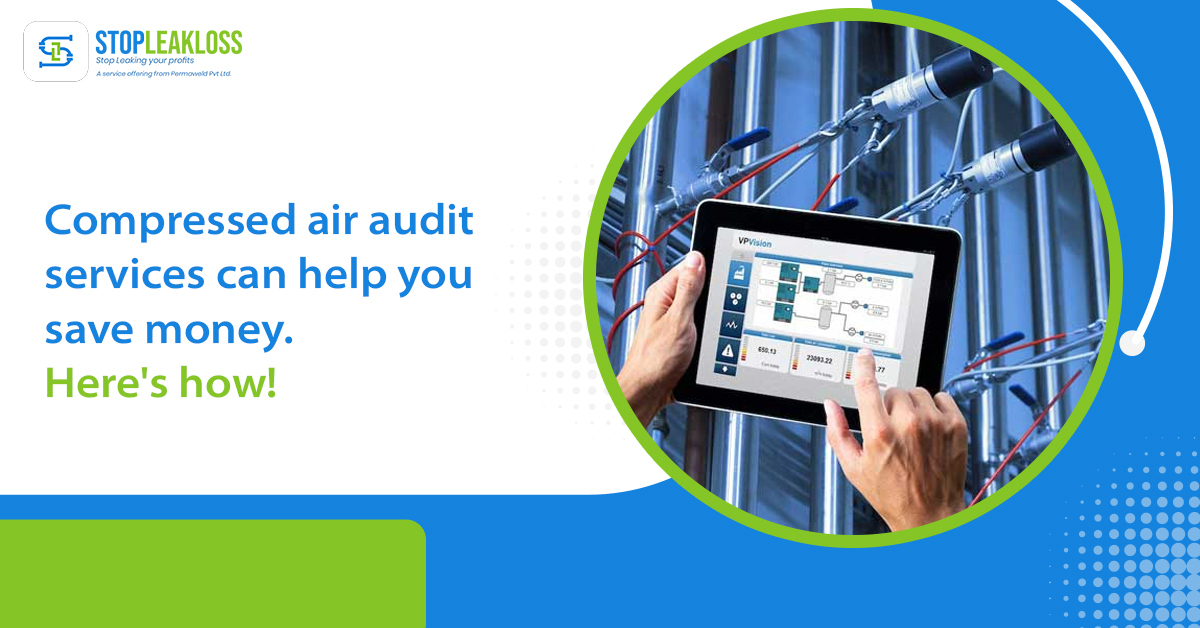
How to design thermal insulation systems
What are the uses of thermal insulation systems?
Thermal insulation is placed in many power stations and industrial units to control heat transfer and conserve energy. Thermal insulation system design entails a number of calculations that can help you determine the best design strategy for the maximized performance of a thermal insulation system. Engineers may construct more resilient thermal insulation systems by understanding the logic behind the basic important and basic aspects related to developing thermal insulation systems. This blog discusses a variety of aspects involved in the design of thermal insulation systems.
Most engineers, architects, and end-users are aware of the use of insulation in buildings or residential structures which is to decrease heat dissipation and maintain cooling and noise control. Mechanical insulation systems for pipes, ducts, tanks, and equipment may be unfamiliar to them. The cost of installing these insulation systems often proves to be considered profitable. In commercial and industrial building projects, however, mechanical thermal is frequently neglected, devalued, or incorrectly designed and maintained.
Thermal insulation system design may be challenging. Insulation systems are used to achieve a variety of design goals. Multiple design goals must sometimes be met at the same time in some projects. On a chilled-water line, for example, the goal may be to reduce energy consumption while avoiding surface condensation. The chilled-water line may go via a number of locations throughout the project. Because the temperature and humidity conditions in different areas may change, multiple insulating materials, thicknesses, and coatings for a single line may be necessary.
For all the small projects, a systematic approach is essential since projects may contain several lines operating at varied service temperatures under various environmental circumstances.
What Fluids Are Being Insulated in thermal insulation systems?
When choosing insulating materials, waterproofing materials, and application procedures for pipe and equipment that handles hazardous substances such as flammable or poisonous compounds, extra thought must be given. Insulation materials that absorb fluids (such as hot oils/heat transfer fluids) and lessen the flashpoint of such fluids should not be utilized in such applications. These services should make use of non-absorbent insulating materials.
For harmful services, non-absorbent insulation materials may be necessary, as the poisonous chemical in the insulation might cause health problems.
Why Is a thermal insulation system Required?
What is the purpose of a thermal insulation system? Because it’s required! Is it required to restrict heat loss for personnel safety, prevent heat gain, limit surface condensation, offer process control, or provide product stability, freeze protection, noise control, and fire protection? Different thicknesses, materials, finishes, and levels of insulation may be required for each of them.
Limit Heat Loss or Heat Conservation
A thermal insulation system alone will not keep or maintain a system’s temperature. The rate of heat transfer through a system can only be limited, conserved, controlled, reduced, or minimized through insulation. However, it will not be able to stop it completely. Insulation is a heat flow reducer, not a heat flow barrier. It’s possible that condensate and blowdown lines to drains or holding tanks should be insulated to reduce heat loss, but heat losses via valves and flanges aren’t vital to the system, therefore they aren’t needed (although personnel protection may be required).
Reducing Heat Gain on Cold Surfaces
The primary goal of installing a thermal insulation system in below-ambient applications is to reduce heat absorption while also minimizing moisture migration or water input into the system. Moisture migration of this nature will have a significant impact on insulation performance. The direction of the vapor driving force causes cold systems to be more susceptible to environmental deterioration than hot ones. The driving force of water vapor in hot insulation systems is away from the hot surface, and while water intrusion into the insulation can have a negative impact on performance, it is usually very transitory. The pushing force of water vapor in cold systems, on the other hand, is inward, toward the cooler surface.
With time, the amount of water that gets into the insulation will grow. Moisture will damage the system over time, eventually destroying it. As a result, by installing vapor resistance and low permeability joint sealants, the whole insulation system design must be comprehensive and well-planned.
Limiting or Controlling Surface Condensation
Thermal insulation systems can be designed to restrict condensation, but not to “prevent condensation” in most circumstances. It’s impossible to create an insulating system that prevents condensation 100% of the time in humid climates. Even the most effective insulation’s needed thickness would be unattainable in these places, both financially and practically.
The ambient temperature and relative humidity, as well as the process operating temperature and surface emittance, are used to calculate insulation thickness. The insulation system should be designed to keep the system’s surface temperature above the ambient air’s dew point. This will prevent condensation from accumulating on the insulation’s exterior surface, reducing the risk of fire and preventing dripping moisture on structures or electrical equipment. It’s critical to agree on the appropriate level of time condensation.
Noise Control
Noisy concerns in the environment can be addressed in the design of thermal insulation systems. Serious noise concerns, on the other hand, should be investigated separately and independently. The insulating design produces sound attenuation as a natural by-product. Some insulation and accessory items provide more sound attenuation than others due to their sound absorption qualities. Mineral fibers are among the greatest sound-attenuating thermal insulation materials.
Sound attenuation can be influenced by the jacketing material used to cover the insulation. Metal jacketing provides superior sound absorption qualities than a fabric reinforced mastic coating over insulation. To minimize noise, metal jacketing can be ordered with a loaded mass.
Fire Protection
Materials in the thermal insulation system for fire protection purposes, on the whole, are more suited for insulation than for fire prevention. The American Petroleum Institute (API) does, however, accept that some insulating materials may give “credit” to the design and size of pressure relief valves in certain circumstances. Insulation system standards are specified by API Recommended Practice 521. The final insulating system must not be dislodged when exposed to the fire-water stream utilized for firefighting, whether by hand lines or monitor nozzles, according to the requirements. The majority of fire-fighting insulation systems are metal-jacketed with stainless steel jackets and bands that fulfill these requirements.
[…] requires especially specialized procedures or processes and appropriate item forms and materials. Thermal insulation materials, known as insulators, are put in commercial buildings to reduce the energy consumption of […]
[…] are many industrial insulating materials to choose from, perhaps too many to list here. Instead, we’ll go through some of the most […]
[…] is the purpose of a thermal insulation system? It’s a necessity under the law! Is it necessary to restrict heat loss for employee safety, […]