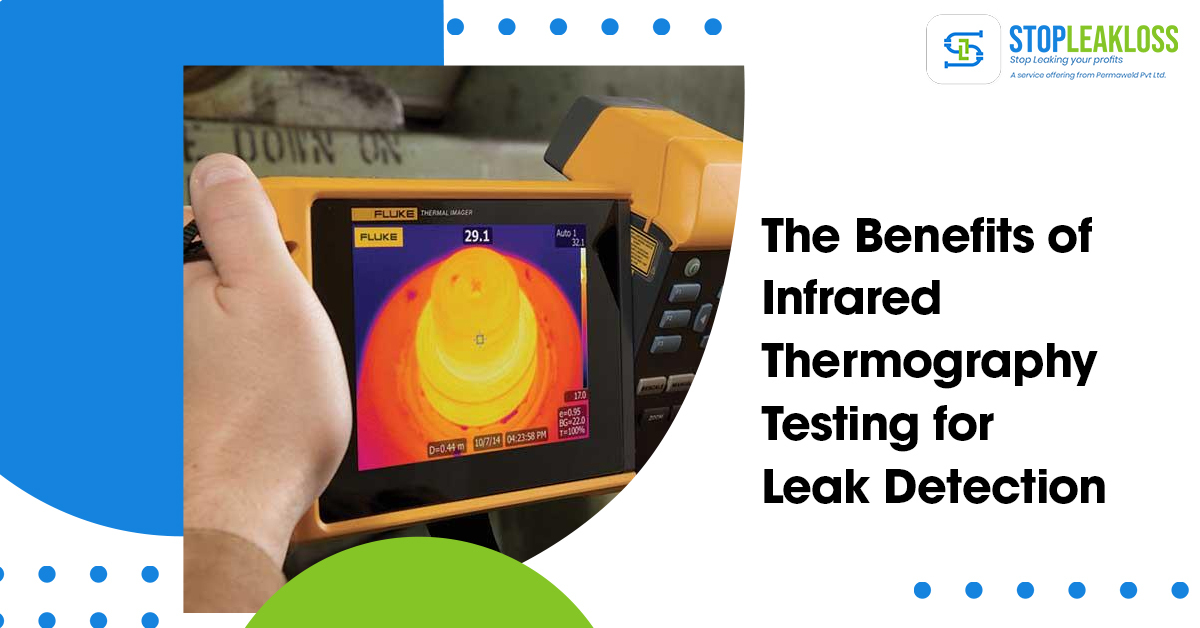
The Benefits of Infrared Thermography Testing for Leak Detection
What is infrared thermography for leak detection?
Infrared thermography for leak detection is the technique of utilising an infrared camera to check for unusually hot or cold spots on a component that is performing normally. It is the most basic of all thermal inspection techniques and a promising non-destructive evaluation approach for the characterisation of corrosion in metallic materials.
Infrared thermography for leak detection has a variety of uses. Thermography is important for detecting corrosion/erosion damage in plants that operate at high temperatures. It may also be used to inspect pipe systems for fouling or internal clogging, as well as to assess the condition of refractory linings. It may also be used to identify leaks, composition changes, and disbonds in laminates. The temperature of things may be seen via thermography. It is a quick, noncontact, wide-area inspection approach that is simple to understand and is not very sensitive to material curvature.
Variants in infrared thermography for leak detection
- Passive: The features of interest are inherently hotter or colder than the background. It has a wide range of uses, including human surveillance and medical diagnostics.
- Active: To create a thermal contrast between the feature of interest and the backdrop, an energy source is necessary. Because the examined parts are normally in balance with their environment, the active approach is required in many circumstances.
What are the benefits of infrared thermography for leak detection
The fundamental advantage of infrared thermography testing over destructive testing procedures is that huge areas may be examined quickly and without requiring destruction during testing. This leads to significant savings in terms of time, personnel, effort, and machinery.
Infrared thermography has additional advantages over other non-destructive procedures. The infrared thermographic instrument is risk-free since it emits no radiation and merely records the infrared radiation generated by the substance being evaluated. Furthermore, infrared thermography is an area investigation approach, whereas the majority of other non-destructive procedures are either point or line testing methods. Furthermore, infrared thermographic testing may be done both during the day and at night.
Another advantage of infrared thermography is its application in condition monitoring. Infrared Thermography in Condition Monitoring aids in the identification of a wide range of difficulties, including heat-related concerns, thermal abnormalities, mechanical issues, and much more. (infrared thermography for leak detection)
Because thermography employs infrared technology, it is not capable of penetrating to great depths. That is, of course, one of the technique’s fundamental drawbacks. Finally, environmental circumstances have a crucial impact on outdoor infrared thermographic studies using the passive technique (i.e. cloud cover, solar radiation, wind speed).
Infrared thermography for leak detection examinations makes use of an object’s surface temperature distribution. There is no sign of a problem if the surface temperature is uniform with no temperature changes. As a result, it has limits in some applications.
Some key highlights or benefits of using infrared thermography for leak detection-
- Inspection can take place during production.
- Inspection is quick and does not require physical contact.
- Results are recorded digitally.
- Costs are relatively low
Applications of infrared thermography for leak detection
Infrared thermography for leak detection provides quick and exact temperature measurement, which is critical for research and testing applications in industrial and academic laboratories. According to reports, researchers used an infrared camera, infrared thermometers, and a multi-colour pyrometer to measure the temperature of individual particles in a coal combustion reactor in order to better understand the transient phenomena that occur when coal particles burn in order to practically design a new low-emission burner technology.
This infrared technology can detect transitory changes that occur in milliseconds, which traditional thermocouples cannot monitor. It is a recognised and authorised sensor technology for measuring, monitoring, and controlling process temperature in industrial situations.
- Injection Moulding: In injection moulding or 3D-printing applications, temperature influences the quality of the end goods. It is critical to get the temperature right in order to ensure that the created items are defect-free. This is especially true in the manufacture of automobile items, where minor dents or faults are not tolerated. The thermal imager was utilised in an online system to measure the surface temperature distribution of the items. It may be combined with a PLC system to automatically reject assemblies if the detected temperature is outside of the defined range.
- Manufacturing: Temperature is one of the criteria that has a significant impact on the quality of manufactured goods in the manufacturing business. For example, the temperature of the molten glass has a significant impact on the quality of the completed glass items. For this reason, a specialised thermal imager for monitoring glass temperature has been designed. Monitoring the temperature of molten metals is critical in the metals business for appropriately maintaining the process temperature during casting. This necessitates the use of a specialised infrared sensor with an appropriate spectral range and rapid reaction time.
- Condition Monitoring: One of the most sought-after technologies as a preventative maintenance tool in industrial process applications is the thermal imaging camera. It may be used for condition monitoring applications, such as detecting hot spots on critical industrial equipment like pumps. Hot areas often signal a problem with the machinery, which might be caused by loose screws, bearing wear, or overheating. Early identification of faults enables for the repair and maintenance of equipment before a catastrophic breakdown occurs, thereby saving the firm lives and money.
Conclusion
Infrared thermography for leak detection is a quick, clean, and safe technology utilised in a wide range of applications. The fundamental concepts and theoretical foundations of temperature measurement and non-destructive testing have been examined. This background material is offered to aid in the diffusion of these technologies and to help newcomers have a better knowledge of the subject. Furthermore, current work on these themes has been evaluated and commented on.
Infrared thermography for leak detection has advanced dramatically in a very short period of time. Significant advancements have been made in a variety of sectors. However, there are some constraints that must be considered. Infrared thermography is highly reliant on sensor selection and experimental settings. It may be influenced by both the instrument and the surroundings. These issues can be reduced, but only with proper setup and testing processes, which are mostly dependent on the operator’s expertise.
[…] don’t have a flow metre and your compressors are in load/unload mode, you can estimate the leakage flow by timing both the load and unload cycles during a period when no production is taking place. […]
[…] Please visit our website STOPLEAKLOSS for more information on our thermal insulation audit. […]