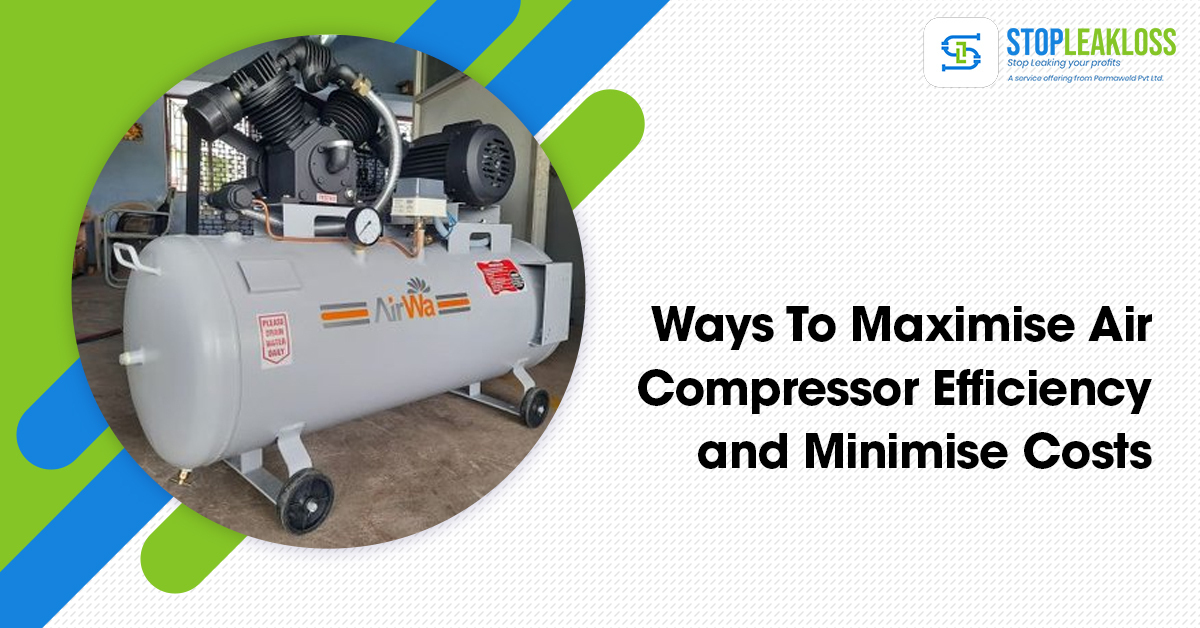
Ways To Maximise Air Compressor Efficiency and Minimise Costs
Air Compressor Efficiency is one of the most expensive kinds of energy for manufacturing operations, consuming significantly more power than other machinery. In addition, electricity is required for every horsepower of compressed air. As a result, there’s often space for improvement, with many air compressors operating at efficiency as low as 10%. Fortunately, 50% of compressed air systems in small to medium-sized industrial operations offer low-cost energy conservation potential.
What boosts the energy efficiency of an air compressor? All elements to consider are type, model, size, motor power rating system design, control methods used, and maintenance schedule. However, the heat loss generated by the higher temperature of pressured air and friction caused by the system’s many moving elements is the main cause of inefficient air compression. (Air Compressor Efficiency)
When it derives to Air Compressor Efficiency, it’s crucial to look at the whole system, which includes the compressor and the supply line. Air dryers, receivers, and after-coolers are part of the storage tank system. You may save a lot of cost & energy by making the correct changes to your compressed air system.
Take into account the requirements for compressed air.
- Take a look at your load profile.
- Reduce the amount of demand that is generated artificially.
- Decide on the proper amount of pressure.
- Make sure that supply & demand are in balance.
- Make use of pressure profiles and block diagrams.
- Make use of compressed air storage.
The following methods will help you increase the efficiency & minimize the cost of your system.
Make the most out of every control on your air compressor.
An air compressor’s controls serve as a link between the compressor’s output and the load requested. Therefore, it’s crucial to match the controls to the equipment’s capabilities. For example, compressors are designed to provide a specific amount of air within a particular pressure range, and the controls determine whether or not they can stop when they reach that range. On the other hand, they define a minimum pressure at which the compressor should restart because persistent high pressure puts a system under more strain—having a fine-tuned control system that can produce usable, steady pressure closer to the minimum required rather than the maximum is preferable. (Air Compressor Efficiency)
Reduce the pressure drop
As compressed air travels through the distribution structure, pressure drops occur. Excessive pressure drops can result in poor performance and higher energy consumption. The end-users lower operating pressure is due to pressure dips upstream from the compressor signal. To fulfil the compressor control parameters, this necessitates greater pressure. Make sure to decrease pressure drops before expanding capacity or raising system pressure. Compressed air equipment should be run at the lowest possible operating pressure for the best results. (Air Compressor Efficiency)
Locate a Cooler near your Intake
When compared to heated air, air requires less energy to compress fully. The system’s performance can be improved by moving the intake to a cooler location. A 20-degree drop in temperature can save up to 3.8 percent on costs. (Air Compressor Efficiency)
Rethink Your System’s Layout
A few easy tweaks to your compressed air system’s configuration can save you a lot of money on energy. Making sure the airflow system is free of bends and kinks, for example, can assist save money and saving equipment from breaking down. Air doesn’t have to work as hard when the distance it has to travel is reduced. Check for any pressure dips in any dryers, filters, or separators. Ascertain that these areas are running at maximum efficiency. (Air Compressor Efficiency)
Maintain a Timeline of Servicing
Regular air compressor maintenance dates are perhaps the most important strategy for maximizing Air Compressor Efficiency over the long haul. It’s vital to keep your machine tuned because of the number of moving parts, the constant flow of air, and the heavy use it gets. In addition, condensation and unclean filters will wear down your system if you don’t take care of it, resulting in a spike in maintenance costs.
Maintenance operations should aim to locate leaks first and foremost. Most air loss and efficiency issues may be traced back to leaks. Even a little damage can waste a lot of energy in an air compressor, putting more strain on the engine and prematurely wearing it out.
Advanced Monitoring
It’s critical to use data when optimizing your system. Advanced monitoring provides you with a clear picture of whether the changes you’re making are saving you energy as well as the amount.
Conclusion
It’s possible that your compressed air system is too complicated for you. If you’ve tried some of the above recommendations but aren’t sure how to proceed, speaking with an experienced technician can benefit you. STOPLEAKLOSS is always willing to assist you in optimizing your compressor setup and making it more efficient. So give us a call right now!
[…] […]