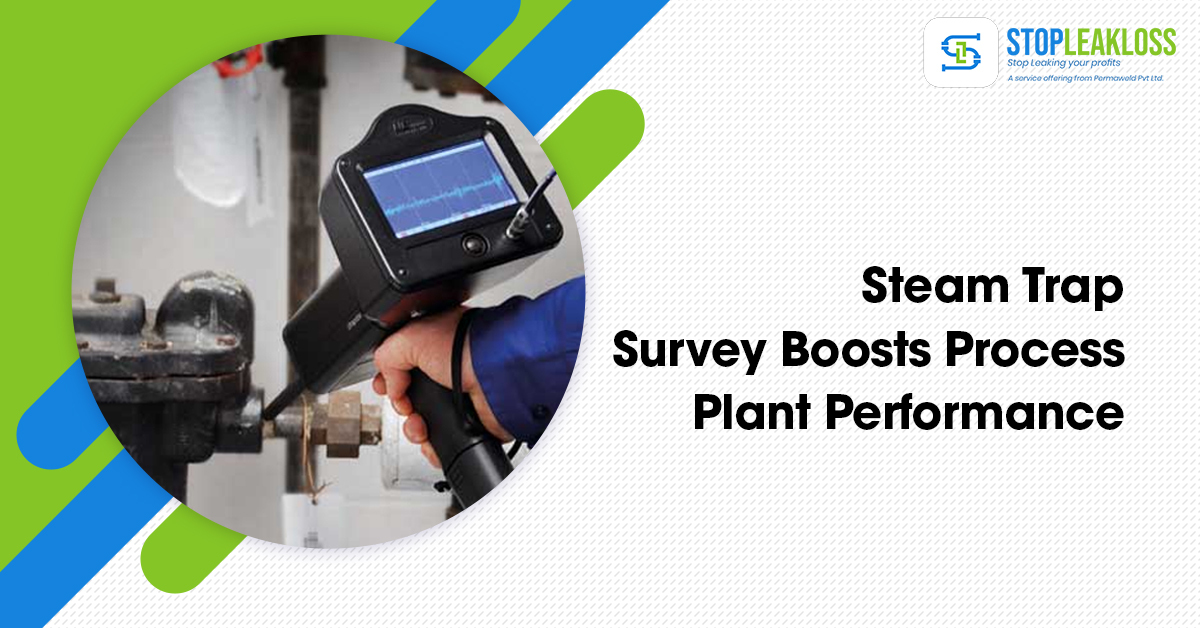
Steam Trap Survey Boosts Process Plant Performance
Steam trap survey, steam is used in various industries as a source of heat and as a mechanical power source. For example, a system boiler provides steam to industries such as breweries, hospitals, food processing, universities, and laundry services. However, for this to happen, boilers must have working steam traps.
Steam traps survey two functions: they filter away condensed steam and non-condensable gases while allowing steam to escape. When the energy from heating the unit is lost, condensed steam is generated. Therefore, it can result in energy loss and physical harm if it escapes and returns to the system boiler. Therefore, it’s vital to do regular steam trap surveys to avoid this.
Experts estimate that steam traps that leak squanders over 20% of the steam produced. A single leaking steam trap wastes around 22 kilograms (Kg) of steam every hour, resulting in 190 tonnes per year. At ₹ 3000 per tonne steam generation costs, this loss amounts to about ₹ 5 lakh per year. The maintenance engineer can employ digital ultrasonic testing techniques to locate and replace broken traps. Before beginning the inspection procedure, you need to know what kind of steam traps you have and how they work, and the system pressure and temperature. In an open system, even the first impression might convey a lot about the condition of the traps.
For example, if there is no condensate at the condensate outlet, this could suggest a problem. The inspector, however, receives a more precise image with integrated temperature and ultrasonic monitoring. Depending on the design, a functional trap opens and closes continuously or intermittently, emitting distinctive ultrasonic signals.
Steam trap survey boosts process plant performance in several ways.
Productivity and Efficiency are increasing.
Steam traps in good working order provide the thermal energy required for industrial applications to function effectively. Condensate in the steam supply can cause issues with application functioning, such as slow start-up times and inefficient heat transmission. However, the steam can concentrate on its function once the condensate is eliminated from the system.
Carbon emissions are reduced, and energy is conserved environmentally responsible.
Condensate typically contains roughly a fifth of the energy in the steam from which it originated. Returning this to the boiler feed reservoir can save thousands of rupees in power alone each year and reduce the requirement for fresh replacement water and expensive chemicals to cleanse raw water. (steam trap survey)
When condensate is collected from the steam system and returned to the feed tank, boiler blowdown, used to manage the concentration of dissolved particles in the boiler, is reduced. As a result, the boiler’s energy loss during the blowdown process is decreased, which helps you meet your overall sustainability objectives.
Profitability
Unwanted condensate is eliminated from the system, which reduces water hammer and corrosion. In addition, steam traps catch condensate as they form, allowing for better steam quality while protecting pipelines and equipment from erosion and corrosion. (steam trap survey)
Well-being, both cognitive and emotional
Like any other plant utility such as hot water or electricity, a steam system must be properly controlled to ensure safe operation. With properly built and operating steam trapping, condensate can be successfully drained from the system, avoiding potentially dangerous conditions like pipe or component failure. (steam trap survey)
Conclusion
As the heating season approaches, the optimum time to inspect your facility’s steam traps is now. Identifying and correcting faulty steam traps will result in a more efficient, proper operating system, which will increase occupant comfort while reducing energy costs. Furthermore, steam trap studies are inexpensive to undertake and result in large overall savings, so this is a no-brainer.
If you’re concerned about any of these typical causes and need expert assistance, schedule a Steam Trap Survey. Then, STOPLEAKLOSS can assist you in increasing plant safety efficiency and reducing carbon emissions.