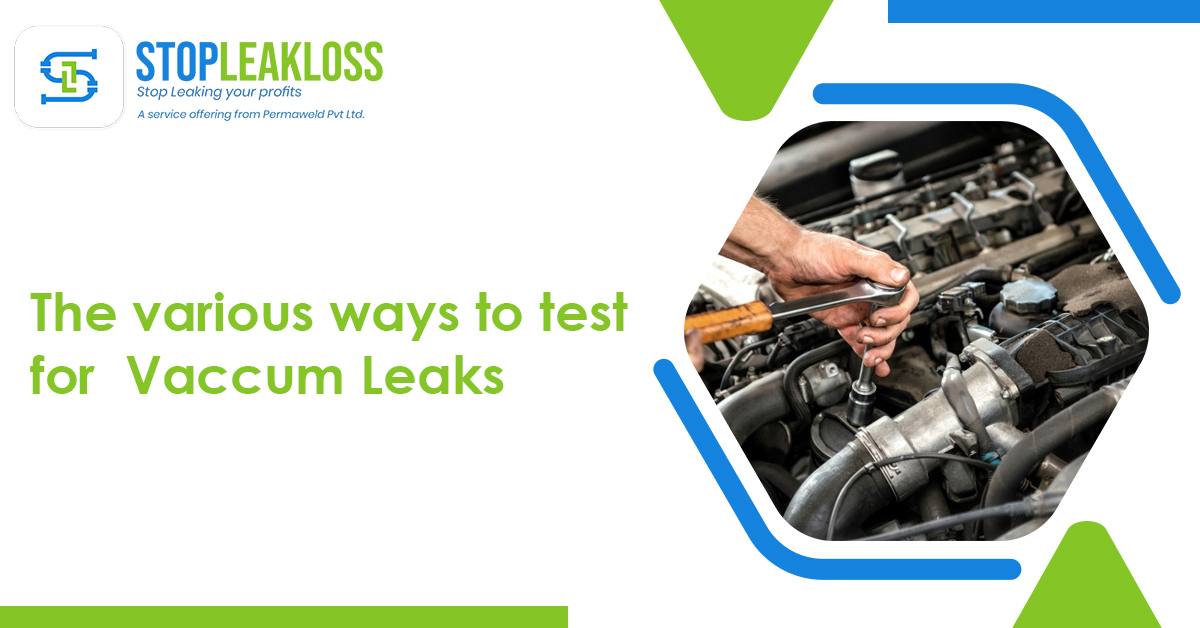
The various ways to test for Vacuum Leaks
Introduction
vacuum Leaks are unwanted openings in the dividers or holes of your items that let solids, liquid, or gases escape through them. Leaks can show up unexpectedly or may foster gradually after some time and harm the quality of the product. If unseen for an extensive period, they might develop to disturb the cycle totally or, to some degree, damage the products. Vacuum leaks influence the vacuum levels in a cycle and hinder procedures in which exact vacuum levels are significant.
When beneficial vacuum levels can’t be reached, leaks are once in a while demonstrated as a limit issue. The most ordinarily realized vacuum leaks are those found in motors. A few strategies can be utilized to identify vacuum leaks in motors as well as different frameworks. Below we discuss some of the ways to test for vacuum leaks.
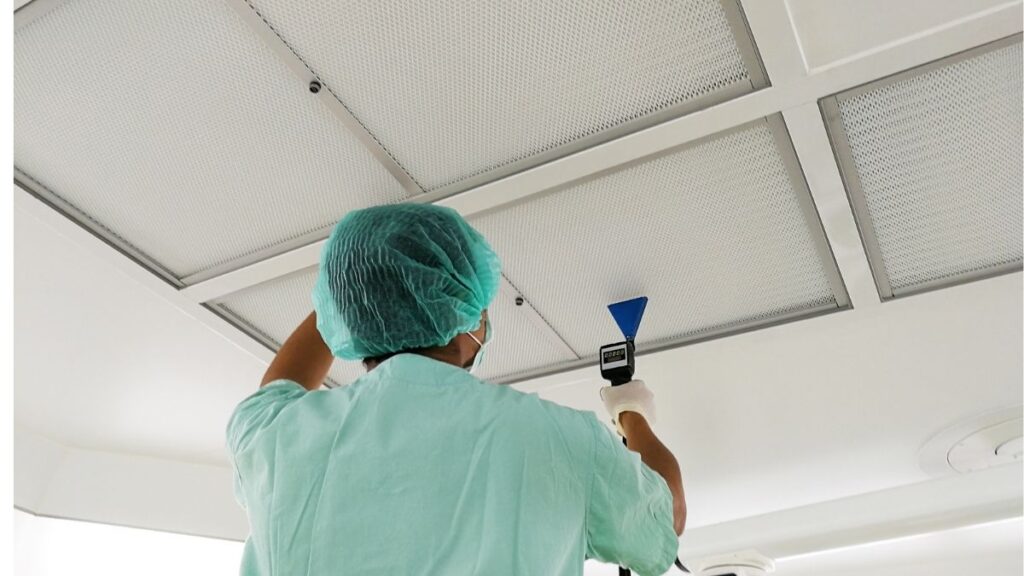
The various ways used for vacuum leak test
Some of the popular methods to test for vacuum leaks include-
- The pressurized soap bubble test- The framework or part to be tried is secluded and afterward compressed. While the framework is feeling, the sudsy squeeze water is applied to potential break destinations and left for a specific measure of time. The regions with sudsy water are painstakingly seen as the leaks cause the foamy water to bubble. The focuses at which air pockets are framed are checked so they might be distinguished for the fix. The compressed cleanser bubble test is the simplest technique for vacuum leak testing.
a vacuum leak means that a certain amount of air has bypassed the usual engine intake tract. Under normal conditions, all of the engine’s intake air is routed through the throttle body.
- The helium identifiers utilize a sensor that identifies the increment in helium fixation noticeable all around the stream. The sensor is set close to the channel of the vacuum siphon, where it can sample the air from the test part. The potential leak destinations are splashed with helium which is immediately pulled inside the framework if there is a leak. The sensor then recognizes the helium, and an alert that shows a break is set off. Helium leak detectors are viewed as one of the most dependable techniques for release testing as they have high affectability and can even find tiny leaks.
- For the parts that cannot be compressed, the flexible tape test can find leaks. A dainty, adaptable tape is put on the potential leak points of the test work. When the focuses have been covered, the vacuum is pulled on the framework, and the tape at every one of the focuses is checked. A leak is identified on every one of the focuses at which the tape is sucked in or scratched. In channeling applications where PVC is utilized for bay funneling, the tapes can be kept set up to fix the vacuum leaks.
- Vacuum leaks are related to a high-recurrence sound. The ultrasound leak detection uses the high-recurrence sound and converts it to a discernible reach that can be heard over a headset. A portion of the locators can likewise show this sound on a meter. A benefit of ultrasonic leak detection is that it very well may be utilized to distinguish between vacuum leaks in compacted air frameworks or lines. Ultrasound leak detection can be performed with tension as low as 1 psi, however higher test strain behind a leak makes it simpler to distinguish and find.
Conclusion
Vacuum leak testing is utilized to test parts that might have leaks from an external source. The vacuum leak test gives better repeatability as it is less responsive to natural factors like temperature change. Different benefits of vacuum leak testing are that it requires little time to arrive at a steady tension, has more limited process durations, and is less prone to the expected precariousness of parts.
[…] Vacuum leaks, for example, can be disastrous for vacuum systems, operators, and the environment if they are not detected early. Therefore, it is critical to design a mitigation plan ahead of time to restore vacuum levels as rapidly as possible. […]