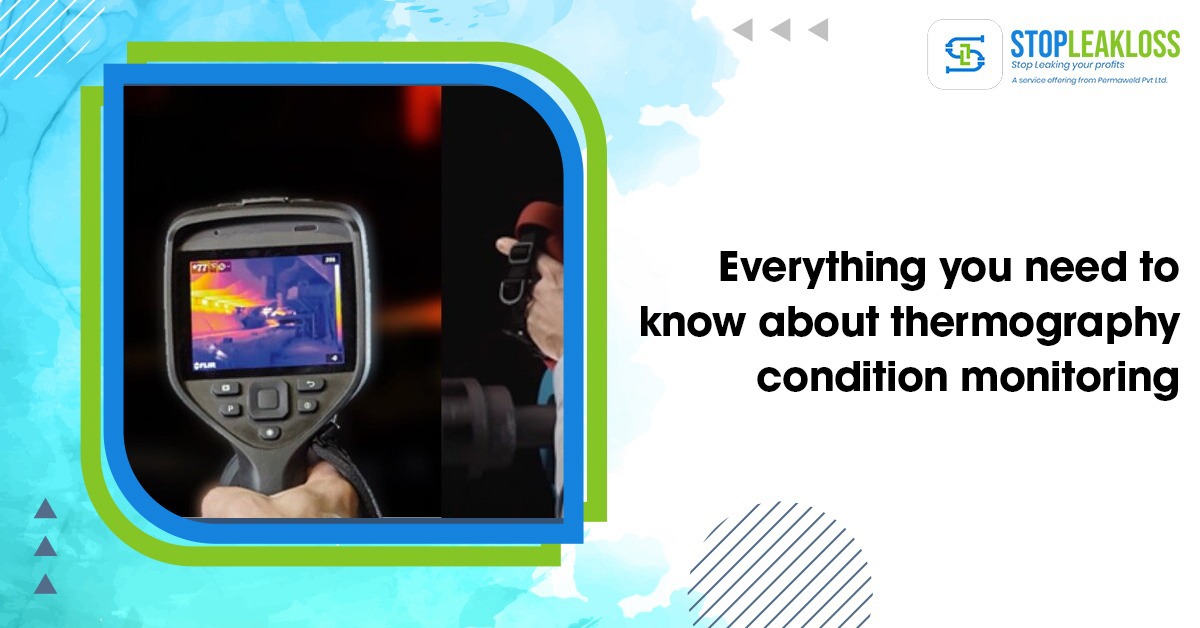
Everything you need to know about Thermography Condition Monitoring
Thermography condition monitoring techniques are used to monitor the temperature and the temperature pattern of operating equipment. This data, along with data on the physical structure of the component and the thermodynamic condition of the equipment, is used to assess the degree of degradation of a process plant item. Three practical applications of thermography to various sectors are described.
Meaning of Thermography condition monitoring
Infrared imaging science is used to monitor the condition of thermography cameras. It is a method of detecting radiation in heat emitted by an object using a thermal imager. It shows a picture of temperature distribution, which is known as a thermogram. We can view heat-producing items that are not visible to the human eye using Infrared Thermography. A basic example is night vision goggles to identify objects in the dark.
Thermography condition monitoring has a variety of uses. Infrared Thermography is widely used in condition monitoring and preventative maintenance. A direct application of this procedure is utilised to determine whether the machine is functioning normally and, if not, to detect the heat pattern within the device, indicating inefficiency and flaws. It is the most acceptable practice for asset management. This strategy decreases risk and improves operational dependability.
Process of Thermography Condition Monitoring
This method is employed in predictive maintenance and condition monitoring. Today we will look at the use of thermography condition monitoring. The notion of thermography condition monitoring is a handy and vital instrument for condition monitoring and preventative maintenance.
Checking bearings and belts, monitoring electrical rooms, energy audits searching for heat loss, fluid handling systems, water leakages, panel boards, rotating motor monitoring, boiler operations, and steam system monitoring may benefit from thermography condition monitoring. This is a technique for pinpointing the specific site of a malfunction in a machine or piece of equipment. We can save energy, money, time, and money on repairs and mishaps that may arise from heat radiation damage. The operations can be handled correctly if we are prepared for future obstacles. Infrared thermography is utilised in various sectors to optimise different production variables.
Thermography Condition monitoring is defined as the measuring of specific equipment parameters, such as vibrations in a machine, its temperature or the condition of its oil, taking note of any significant changes that could be indicative of an impending failure. Continuously monitoring the condition of equipment and taking note of any irregularities that would normally shorten an asset’s lifespan allows maintenance.
Benefits of thermography condition monitoring
There are several benefits of thermography condition monitoring, mentioned below are some of its benefits concerning Condition Monitoring
- Can detect heat-related problems: Infrared Thermography prevents unanticipated malfunctions that might impede or hinder operations, knock off power, and even start a fire. The method of infrared thermography measures the energy emitted by an item and detects heat-related concerns before they become a disaster for everyone.
- Easily detect thermal anomalies: Infrared Thermography identifies excessive heat generated by severe loading, incorrectly sized component utilisation, load imbalance, or resistance caused by faulty connections.
- Mechanical issues:Thermography condition monitoring detects mechanical defects such as faulty lubricants, misalignment, or other friction-related problems. As a result, this Thermography technique is critical in meeting the impending difficulties of the industrial and other industries.
- Cost reduction: We may save money on business disruptions caused by breakdowns, downtime, electric fires, challenges connected to electrical and mechanical concerns, and so on by using the crucial instrument of thermography condition monitoring. As a result, it saves both money and time, which benefits the entire manufacturing unit. It also saves money on repairs.
- Minimize Unplanned Downtime: All process industries strive to reduce unexpected downtime, not only because of the high direct cost, but also due to the disruption that occurs, obstructs the production line, and ultimately has a negative influence on the business. In many circumstances, this new thermography condition monitoring system may identify changes in equipment health far before failure, giving maintenance workers plenty of time to arrange an inspection, investigate, and, if required, correct the problem.
- Support ongoing reliability: The application of thermography condition monitoring in various industries increases the dependability of the industry’s working and production processes. This procedure and therapy are risk-free for all personnel and equipment.
- Risk reduction: Overall risk decreases since workers and management may now plan ahead of time to correct the problem by checking and investigating with Infrared Thermography.
Conclusion
Thermography condition monitoring offers numerous advantages, including 24*7 remote monitoring, early warnings of potential (serious) failures, reduced unplanned downtime, lower maintenance costs, ongoing reliability support, and risk reduction with fewer inspections at heights, confined, and remote assets. It also helps reduce the stress level of maintenance personnel in process industries.
[…] ENERGY BY Thermal Insulation Audit in YOUR […]
[…] condition monitoring or thermography condition monitoring (CM) is a technique for ensuring machine health and safety by utilizing sensors and software tools. […]