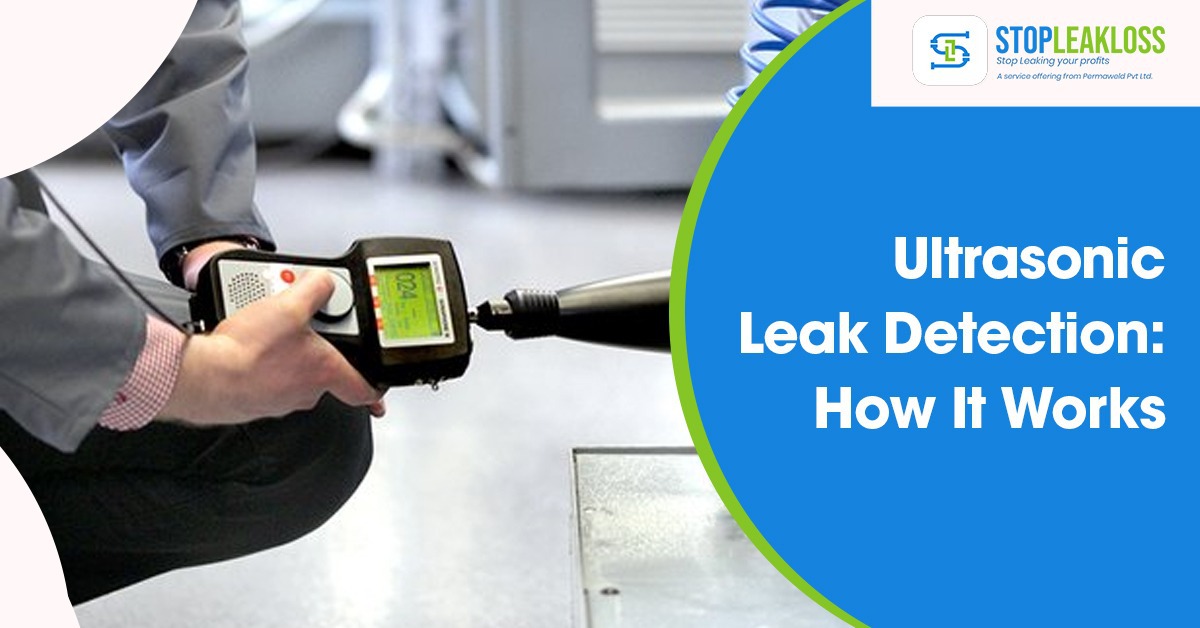
Ultrasonic Leak Detection: How It Works
What is Ultrasonic Leak Detection?
Sound is particularly sensitive to ultrasonic leak detectors. A high-quality ultrasonic leak detector, when correctly calibrated, will allow users to hear the blink of a human eye. This sort of leak testing may be done in an open or enclosed space and can be calibrated to isolate the sound generated by the leak. Because ultrasonic leak detection concentrates on a specific frequency range of sound, wind noise, voices, traffic, and other regular operating noises may be filtered out. It will not impair the test’s accuracy. Ultrasonic detectors can detect pressure and vacuum leaks depending on the application.
More significant leaks are usually louder, have a lower frequency sound, and are simpler to find than minor ones. Ultrasonic Leak Detections employ a microphone system that detects sound created by leaking gas at frequencies ranging from 38 to 42 kHz. Unfortunately, some acoustic leak detection equipment is confined to an isolated frequency bandwidth; these instruments may sound false alarms for non-existent leaks or fail to detect a leak at all. Quality ultrasonic detectors employ an electrical technique known as “heterodyning” to convert high-frequency leak noises to a lower range, allowing a hissing leak to be heard through headphones while manually adjusting the microphone to locate the leak. (Ultrasonic Leak Detection)
How does Ultrasonic Leak Detection work?
Ultrasonic leak detectors, as the name says, detect the ultrasonic sound of a leak. You’ve probably heard the hissing sound made by a massive leak. More minor leaks produce sound, but the frequency is too high for human ears to notice. Ultrasonic Leak Detectors use a heterodyning technique to convert the ultrasonic hissing sound to a lower frequency that can be heard using headphones, guiding you to the source. As you move closer, the music becomes louder and/, or the LED metre grows.
Reduce the sensitivity as you get closer to the leak to make it easier to find. Some leaks can be heard from many feet away. Thus direct access to the leak is not always required. As long as the leak is turbulent, enough sound will be detected ultrasonically. Ultrasonic Scan detects pinhole leaks as low as one psi. However, the more pressure appears behind the leak, the more turbulence there will be present, and the easier it will be to locate.
Ultrasonic Leak Detectors are most sensitive to noises at 40 kHz, which is double the frequency of human hearing at its finest. When a turbulent gas escapes, it generates ultrasound, making no difference in what gas you are measuring. Ultrasonic can detect air, nitrogen, fresh or old refrigerants, or even air as it rushes into a vacuum-sealed system.
Ultrasonic Leak Detectors are so sensitive to sound that they can detect the blink of a human eye, although they are not gas specific. For example, a leak test can be performed in an enclosed environment saturated with refrigerant, and the only signal provided by an ultrasonic is the sound of the leak. However, because the ultrasound is focused on a specific sound band, wind noise, voices, traffic, and most regular operating background noise will not be heard.
How do Ultrasonic Leak Detection systems work collectively?
First, the transceiver for Ultrasonic Leak Detection provides a current to the transmitter instructing it to generate a burst of 40 kHz sound. This sound goes throughout the compartment, such as the cargo hold, reverberating throughout the space. In general, the sound waves will return to the device and be detected by the receiver.
When there is a leak or gap, sound waves will reverberate differently or not at all, instead of escaping through the breach. This results in a loss of good energy, which is transmitted back to the receiver and recorded by the transceiver. When the transceiver detects an abnormality, it will notify you through headphones. An audible sound will provide you with the information you need to establish a leak and where it is located.
Furthermore, the inspection of microphones’ telescopic structure of Ultrasonic Leak Detection allows for a comprehensive examination of a specified region. This is especially valuable for evaluating seams and welds in difficult-to-access areas, where the difference between a solid hold and one that enables water to enter might be significant.
Water damage costs the transportation sector millions of dollars each year, but thanks to our Hatch Sure cover tester, our clients are significantly decreasing these losses. In addition, our dependable and innovative technology provides our customers with the peace of mind they require to confidently send their ships out with valuable cargo, knowing their cargo hold is safe.
[…] great majority of air loss and efficiency issues. Even a little one can waste a lot of energy in an air compressor, (air compressor maintenance tips) placing extra pressure on the motor and leading it to wear out […]