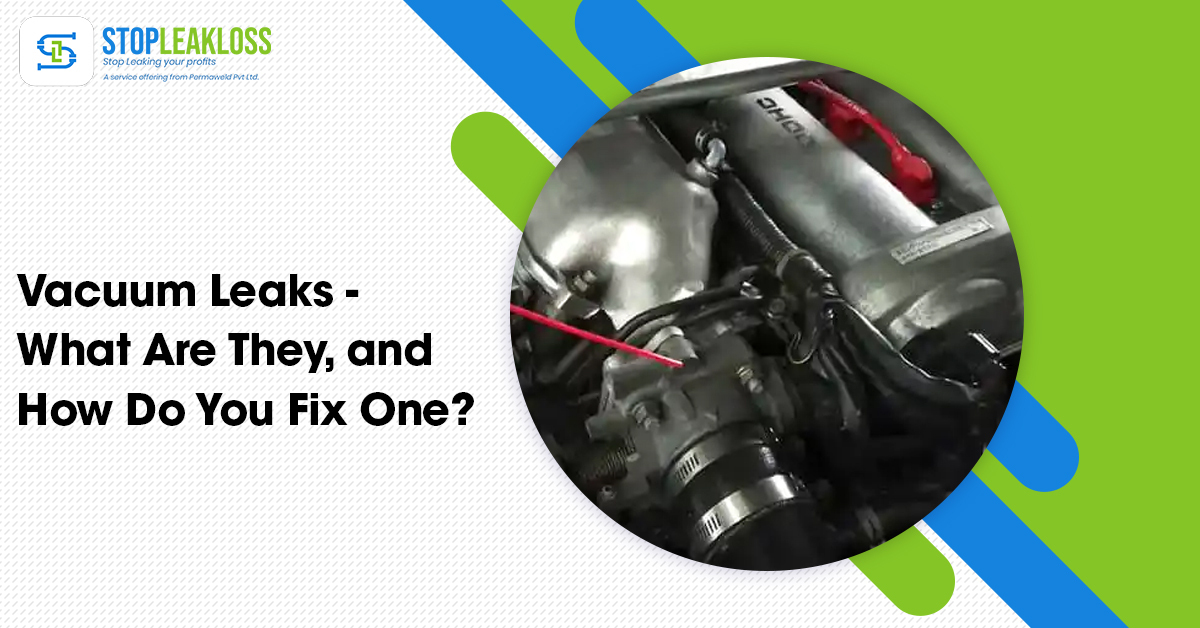
Vacuum Leaks – What Are They, and How Do You Fix One?
The vacuum systems and pumps utilised in every operation that requires vacuum—especially where very fine instruments are involved (R&D mass spectrometry)—have even less margin for error than ever before as vacuum technology applications evolve and become increasingly exact.
Unexpected problems in a vacuum can be disastrous for the process, the environment, and the operator, and one such situation that can be challenging is a vacuum leak.
Vacuum leaks, for example, can be disastrous for vacuum systems, operators, and the environment if they are not detected early. Therefore, it is critical to design a mitigation plan ahead of time to restore vacuum levels as rapidly as possible.
Vacuum leaks are minor breaches in the system that allow fuel to escape or enter without permission. The size of the hole, the temperature, the type of fuel being pumped through the system, and the interior vs outside pressure differentials all influence the severity of the leak.
When a vacuum system leaks, it reduces efficiency and puts personnel and products in danger. A vacuum leak can have a variety of detrimental consequences, including the following:
- Leakage of toxic substances into the environment
- Entrance of a contaminant
- Harm to the system
It’s worth noting that vacuum systems don’t have to be vacuum-tight to function well. However, they must maintain proper operating pressure, fuel balance and achieve and maintain maximal pressure.
Indications
The Check Engine light, stalling, a rough idle, & a hissing sound from the engine bay indicate a vacuum leak. At higher RPMs, the engine performs admirably, but at idle, it surges, runs rough, and struggles to maintain constant RPMs. Stopping often causes the engine to stall. According to a diagnostic tool, the Long Term Fuel Trim (LTFT) heading towards the plus (lean) side at idle but returning near to zero at higher RPMs is one of the symptoms of a vacuum leak. This means the engine is running lean at idle.
VACUUM LEAKS: HOW DO YOU DETECT THEM?
This entails submerging a punctured bicycle tube and identifying the source of the bubbles or putting washing up fluid around the joint of an active gas/water pipe to see where the bubbles/foam originate.
- This test is carried out by removing air from a closed vacuum vessel until a specified pressure is obtained. The pump’s inlet valve is then closed and then opened after some time. If the time it takes to return the vacuum to its previous level remains constant after multiple repetitions, there is a leak. Conversely, if this period shortens, gas will most likely be removed from the system’s interior, although a leak is still possible.
- The pressure decay test is the inverse of this test. It entails comparing the time it took to reach a certain vacuum level to its time to get there. If there is a leak, the curve will become a straight line after isolating the system. Afterwards the pump has been turned off & the pressure has been dropped to a certain level, it’s a good idea to keep a check on the force. There could be a leak if pressure builds continuously. However, strong degassing from liquids or vessel walls also raises pressure; therefore, detecting a breach isn’t a foolproof method.(vacuum leaks)
- The only way to detect a smaller leak is to use a Helium test, which is popular not just for its capacity to detect small vacuum leaks, but also because it’s light (low mass), fully inert/non-reactive (and safe), and inexpensive.
A Vacuum Leak is a problem that requires immediate attention.
It’s time to move on to the repair step when a tester has identified a vacuum leak and calculated its leaking rate. Repairs won’t make the system leak-proof, but they can get the vacuum performance back to where it needs to be for the system to function properly.
Vacuum Leak Repair in View Glass and Feedthrough
The feed-throughs and view panes are either bonded or welded together. Therefore, mechanical stress or temperature cycling can cause a leak at the junction between these and other materials over time. (vacuum leaks)
View glass and feed-through vacuum leaks are notoriously difficult to repair. In most cases, the parts will need to be replaced. However, low-degassing resins can be used to patch view glasses and feed through in some cases.
Welding the leak to guarantee that the system is tight is the best approach for vacuum vessel bodies or port welding. To prevent degassing in high-vacuum tanks, weld from the inside. (vacuum leaks)
Vacuum Leak Repair After a Seal Failure
Component joints—the system’s seals, for example—are where most vacuum system leaks occur. Pump lines, chamber doors, and electrical feed-through regions are frequent places for leaks to occur. In addition, all seals will become brittle after a few years of use and wear. (vacuum leaks)
The leaky seal has to be replaced, a reasonably simple fix.
Is it Costly to Fix a Vacuum Leak?
The cost of repairing a vacuum leak is determined by several factors, including the leak source & how difficult it is to pinpoint the leak. Replace a vacuum hose or replace the intake manifold to fix the problem.
[…] This blog shows you how to locate a vacuum leak. […]