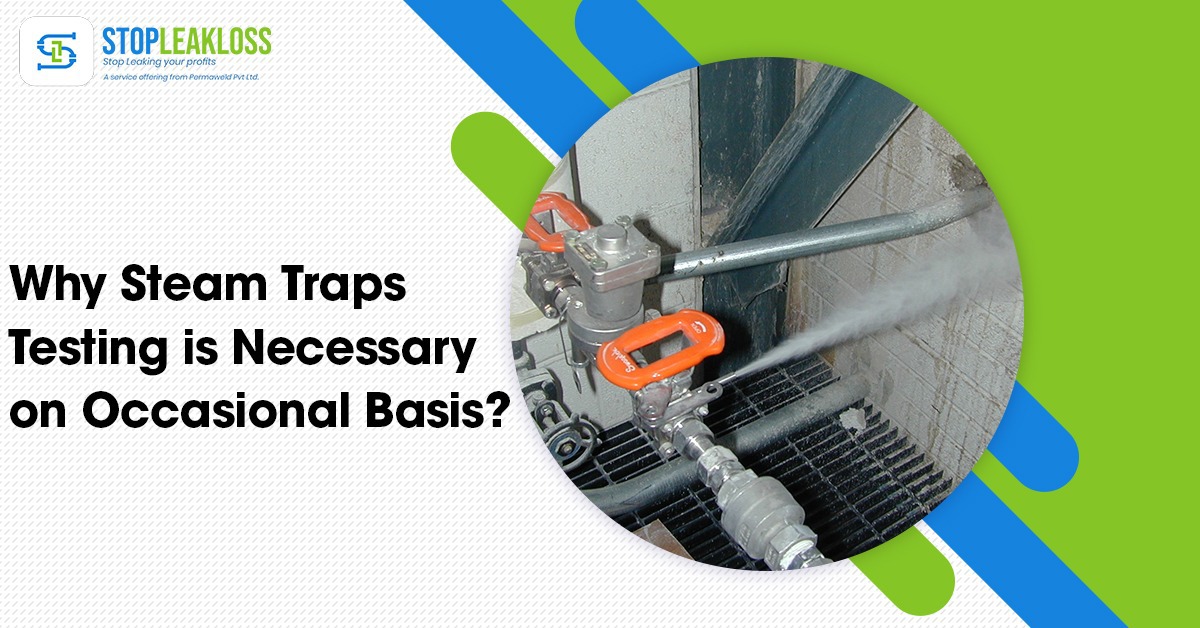
Why Steam Traps Testing is Necessary on Occasional Basis?
Steam trap testing- Steam generation costs a lot of money and energy; therefore, running your steam system as effectively as possible is a good idea. Checking to see if your steam traps are in good working order is smart to start. Steam traps are atypical and essential components of any steam-generating industrial plant. As a result, accomplishing the most out of steam traps and optimising plant production is critical for plant managers. Even one leaking steam trap can result in significant steam and income losses.
If temperature fluctuations cause steam traps to open too frequently, the added wear and tear will certainly demand repair regularly. On the other hand, if steam traps aren’t opened regularly enough, and condensation builds up, this creates a new problem.
Typical space heating systems without a steam trap monitoring system lose 20% of the steam exiting a central boiler plant due to leaking taps. In addition, between 15% and 30% of installed steam traps may have failed in steam systems that have not been serviced for 3 to 5 years.
So it’s very important to test Steam traps on an occasional basis
The precise identification of defective traps has always been a serious challenge. Faulty traps can be left unattended, while perfectly good traps are replaced unnecessarily if the diagnosis is incorrect. (steam trap testing)
As a result, each steam trap testing programme must begin with a precise diagnostic.
Visual observation, temperature measurement, sound or ultrasound measurement, and some combination of these methods are used for steam trap testing to determine if it is working properly.
Visual Observation
While limited in scope, visual observation is a critical first step in establishing whether or not a trap is working well.
Certain visible signals, such as a lack of condensate discharge or exceptionally large amounts of steam seeping from a trap, may indicate that the trap needs to be repaired. A visual inspection is, of course, limited to looking at open systems. For example, the pipe will preclude visual diagnosis when recovering condensate in a closed piping system. In rare cases, installing a sight glass at the trap’s outflow may be beneficial.
Pinhole, connection joint, and gasket leaks can also be checked outside. However, testing traps by sound and temperature, and in some circumstances, thermography, will be required to make a correct diagnosis in most cases unless a condition problem can be easily recognised visually.
Temperature Measurement
The first stage in the steam trap testing process determines the temperature falling of the trap’s inlet condensate. Therefore, the condensate temperature at the trap inlet should be around that of saturated steam, unless in circumstances of purposeful subcooling (such as specific low-temperature tracing).
Using temperature to evaluate whether or not a steam trap is leaking can lead to inaccurate results. Higher temperature condensate flashes into steam when put into a lower pressure system. The measured temperature cannot distinguish between a steam leak and a typical condensate discharge since the flash steam temperature is identical to that of leaking live steam.
Sound or Ultrasound Measurement
Most traps’ opening and shutting valve mechanisms, as well as the condensate pouring through them, cause sound and vibration. These sounds will often change when a trap is no longer working as it should (due to wear, obstruction, or other factors). One approach to evaluating a steam trap’s condition is to recognise this discrepancy. (steam trap testing)
Scale and other floating debris, for example, can obstruct the vent hole in bucket traps, causing the inverted bucket to jam shut, at least temporarily, resulting in blocked discharge and freeze-ups in some situations. The distinction between a “whistle and a wave” can be explained by live steam pouring from a trap producing a unique sound. Even when made lightly, a whistle is a vapour-based, high-pitched sound. It is impossible to replicate the same sound even with a liquid, vast, wave or as small as a drip from a faucet.
The sound of condensate passing through a trap should be lower in pitch. So, if this sound changes and becomes much more similar to a higher-pitched sound like steam flow, the trap may have a lot of flash steam or be leaking live steam and must be inspected further.
Conclusion
Steam trap testing is an important aspect of steam trap management. The trap should be fixed or replaced as quickly as feasible when failure is established to get the best results.
At STOLEAKLOSS, we employ cutting-edge technology created by our Japanese partner, TLV, specialising in steam trap testing. The survey approach is a mix of software and hardware, with hardware doing the fieldwork and software handling the data analysis.
Contact Us For more information.
[…] Warhammer and corrosion are reduced when unwanted condensate is removed from the system. Steam traps collect condensate as it occurs, allowing for higher-quality steam while also safeguarding piping and equipment from erosion and corrosion. (steam trap survey) […]
[…] of the utmost environmentally friendly forms of insulation is cellulose insulation. Cellulose comes in a loose form and is created from recycled cardboard, paper, and other similar […]