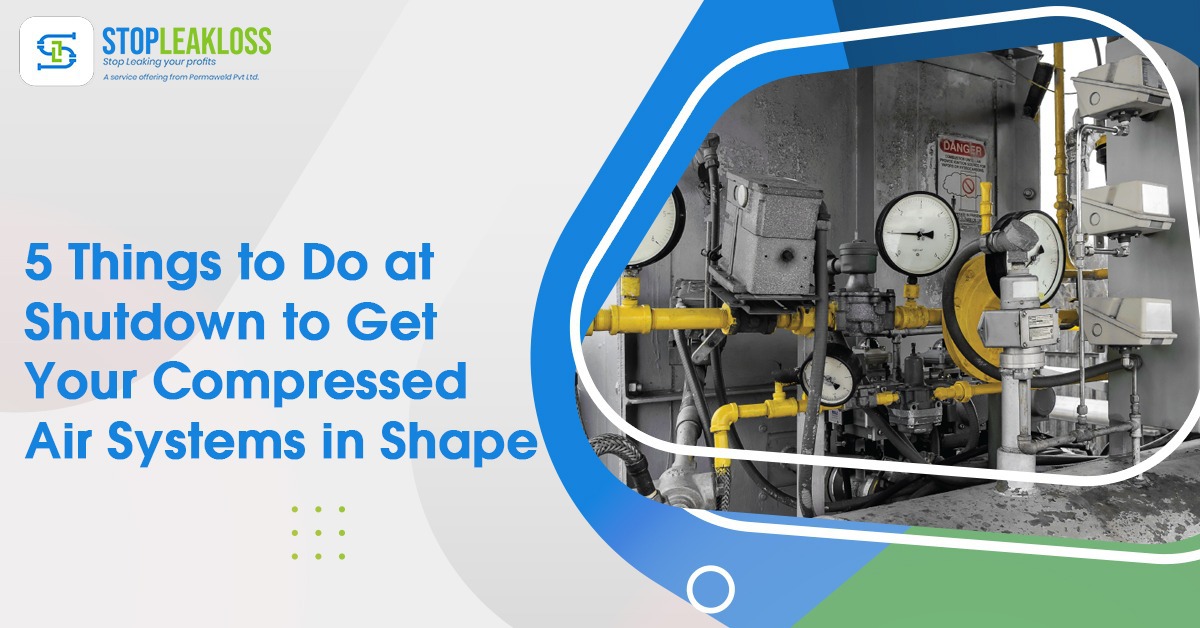
5 Things to Do at Shutdown to Get Your Compressed Air Systems in Shape
Compressed air systems- Air leaks are your compressed air system’s biggest adversary, regardless of the outside temperature. Your business air compressors may be clear of contaminants (such as moisture or oil) and have excellent filtering capabilities, yet an air leak will cause them to fail. Air leaks can occur anywhere from your machine to the end of your distribution network, and they can lose up to 20-30% of the compressor’s output. (compressed air systems)
If you know your leak but can’t discover it, don’t just turn it on! Some people increase the pressure to attempt to find the leak. This is not recommended since it might harm your compressed air system. One of the primary advantages of frequent inspections is the detection of these leaks. Once you’ve identified the leaks in your compact air system, seal them up to guarantee a smooth and safe shutdown. Remember that unattended leaks might reduce the service life, require more maintenance on supply equipment, or require air compressor replacement. (compressed air systems)
1. Perform routine maintenance repairs
This may sound like a no-brainer, but you’d be shocked how many facilities don’t schedule or undertake scheduled maintenance when a shutdown is available. Consider the following tasks for your shutdown- Change the oil and oil filter, the air filter, the filters on the dryers, and collect oil samples. (compressed air systems)
The simple act of changing the oil and detecting any pollutants might provide insight into additional troubles that the machine may be experiencing before they become problematic! Next, clean the oil cooler and aftercooler, which helps the compressor retain optimal performance and lowers output temperatures, so your compressor doesn’t have to work as hard. The issue with filthy aftercoolers is that they transmit hot air and unneeded condensation downstream to your dryer. (compressed air systems)
2. Keep dryers under inspection.
Dryers tend to underperform when the air entering them is either hot or damp. This takes us to our next piece of advice: thoroughly check your dryer. Dryers use large quantities of energy to play a significant role in one of your plant’s most essential utilities. However, depending on the dryer you have, the processes are slightly different. Start with verifying the dryer is cycling correctly and testing the desiccant quality for desiccant dryers.
Next, refrigeration dryers- Is the device hitting the desired dew point? Is the Compressor outlet temperature low enough to allow the dryer to function efficiently? If the dryer isn’t switching its setpoint, is overheating, or freezing, have a technician knowledgeable with refrigeration inspect the refrigeration compressor. Dryers should be examined and cleaned regularly, like air conditioners, but this is an often forgotten element of a utility plant’s preventative maintenance. (compressed air systems)
3. Keep a check on your distribution systems
It should be evident by now that moisture is your air system’s biggest enemy. Unfortunately, the distribution system is another excellent hiding spot for unwanted moisture. To fight this, begin by opening and examining all drains and Zero Loss Traps for proper operation. First, check to ensure that no condensation has built up in your air system, including wet and dry storage tanks.
Next, check if any of your drain valves are jammed open or closed. If your condensation drains are on a timer, consider replacing them with the more efficient zero loss drain valves. As the name implies, these valves combat leaks even more effectively, saving your system vital compressed air. Unfortunately, condensation buildup is a common cause of distribution system problems, necessitating periodic maintenance.
4. Have a backup compressor in place
It’s no secret that compressed air is critical to the efficient running of your power plant. Have you ever considered what might happen if your compressor failed? In the case of a compressor failure, you must have a backup compressor up and operate as soon as feasible. Even if your facility has backup compressors, a catastrophic failure might force you to scramble at the last minute during minor outages. Consider adding a tie-in point for continuous compressed air during a regularly planned compressor outage to save yourself time and headaches. Tie-ins make bringing in a new or rental unit a breeze. (compressed air systems)
5. Keep spare repairing essentials.
Planning for your next shutdown is the best approach to remain ahead and keep your mechanical equipment running smoothly. The easiest method to accomplish this is to have all the necessary supplies on hand. Having an adequate supply of these goods on hand at all times is critical to a smooth shutdown: oil, oil filters, air filters, and oil-water separators. (compressed air systems)
When done correctly, shutdowns show to be a key component of your plant’s lifetime and can boost profit margins in the future.
[…] minor ones. Ultrasonic Leak Detections employ a microphone system that detects sound created by leaking gas at frequencies ranging from 38 to 42 kHz. Unfortunately, some acoustic leak detection equipment […]
[…] in the compressed air systems and come up with solution-oriented procedures and equipment for compressed air audits. To guarantee that compressed air systems are used more efficiently, our team of specialist […]