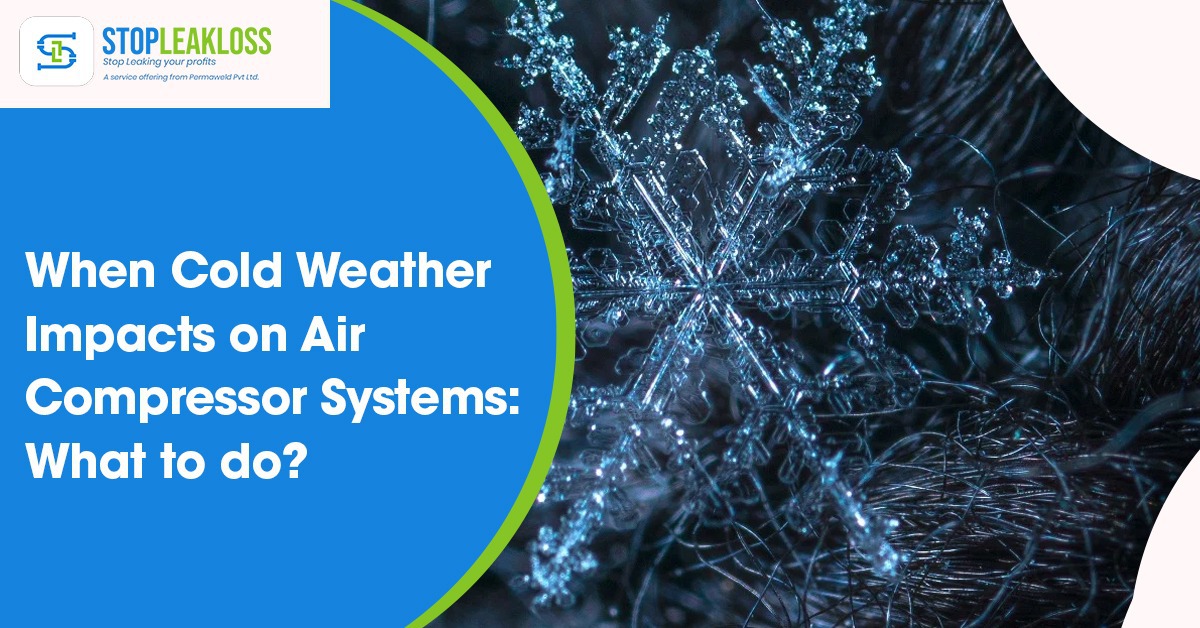
When Cold Weather Impacts on Air Compressor Systems: What to do?
Did you know that the optimal working temperature is between 40° and 95° Fahrenheit? This implies that the freezing temperatures of winter can significantly influence your compressed air system, especially if the ambient temperatures in your compressor room are below this range. So, it’s time to investigate what the well-known expression “Winter is Coming” implies for your air compressors!
How Does Cold Temperatures Impact Air Compressor Systems?
Cold winter temperatures can harm your air compressors in both the short and long term. Frozen condensate, for example, might clog/crack essential components within the more extensive compressor system. In addition, control lines, drain valves, compressed air filters, and heat exchangers are also at risk of freezing and cracking. Other potential consequences of chilly ambient temperatures include:
- The air compressor does not turn on. Do you have a rotary screw compressor that won’t start in the cold? There’s a fair likelihood this is due to the low ambient air temperature limit switch (which many screw compressors have), which prohibits the compressor from starting if the ambient temperature falls below 40 degrees Fahrenheit.
- The oil of an air compressor is becoming thicker. The heavier the oil, the colder the temps! More viscous compressor oil has less lubricating capabilities, requiring more power to run the pump. Keep a watch on this — if this happens for an extended time, the motor’s lifespan may be reduced.
- Refrigerated air dryers are too efficient. Refrigerant air dryers run the risk of overheating; when moisture is extracted from compressed air, it can freeze and harm the larger drying system.
- Desiccant Air Dryers’ Drying Capacity Has Dropped. Wet incoming air locations can cause desiccant air dryer pipes to freeze, causing tower switching valves to fail. The discharge air purge mufflers can freeze, resulting in decreased purge airflow.
- Corrosion of Components Because air dryers are less effective at cooler temperatures, there is a larger possibility of increasing condensate throughout the compressor system. As a result, internal components are more likely to rust and corrode as time passes and moisture levels rise.
Tips for Prepping Your Air Compressor for the Cold Weather
- Condensate should be drained. In air compressors, condensate is a regular occurrence. It originates in the system and settles in low locations like tanks. In the winter, untreated condensate can freeze and burst pipes. It’s critical to examine your tanks multiple times each week throughout the winter and year to avoid condensation accumulation. If even the tiniest quantity of moisture collects, drain it quickly. When there is a lot of moisture in your system in a short period, it might be an indication of something far worse. You should also think about adding an automated drainage valve; it’s a simple remedy that will save you money on major problems.
- Outside pipes and condensate drain should be winterized. If temperatures in your region are forecast to dip below freezing, wrap heat trace tape around any exposed drain lines to keep them from freezing. Insulate any outdoor pipes as well!
- Icy Oil and Frozen Water One of the most problematic difficulties that seem to develop when temperatures dip below freezing is water and oil. It is critical to conduct timely assessments of any point where liquid might be separated and identify any potential spots where leaks could occur. Oil temperature should also be checked and managed; otherwise, the oil might become too cold to lubricate or seal the equipment. Icy oil can also cause a compressor to fail or cease operating entirely.
- Warm-up your compressor. If your compressor is in an unheated area, a modest space heater can provide extra heat to keep the temperature below 41°F.
- Make use of Trace Heating. Trace heating on pipes can assist keep the air compressor and distribution system from freezing. This is especially critical if any pipes travel through cold or outdoor regions to freeze and send ice particles down the line to end-users.
- Understand Your Dew Points. The winter months necessitate a lower dew point. A compressor that performs well throughout the day may not be adequate after night! Some facilities also feature compressed air systems that send compressed air from one location to another via lines within and outside the facility. The technology in these plants handles two different temperatures simultaneously using the same equipment. In general, the dew point of a compressed air system should be set at least 20 degrees below the lowest forecast.
Need assistance in preparing your compressor system for winter? We can help. Reach out to stopleakloss today!
[…] power plant. Have you ever considered what might happen if your compressor failed? In the case of a compressor failure, you must have a backup compressor up and operate as soon as feasible. Even if your facility […]